As an important resource mineral in the new energy industry, lithium ore beneficiation is very critical. In the lithium ore processing process, in order to obtain better beneficiation effects and achieve ideal recovery benefits, there are four key points that need to be paid attention to, namely the particle size distribution of lithium ore, lithium ore desliming treatment, beneficiation water quality, and lithium ore flotation bubble. Below we will expand on these four aspects one by one.
Use the table of contents below to navigate through the guide:
01Grain size distribution of lithium ore
The particle size distribution of lithium ore has a significant impact on the lithium ore processing process. Particle size distribution, that is, the distribution of particles of different sizes in the ore, is one of the key factors that determine the processability of the ore and the efficiency of mineral processing. The particle size distribution determines the difficulty of the ore in the grinding process. The ideal particle size distribution can enable better monomer dissociation of ore, reduce over-grinding and under-grinding, thereby improving grinding efficiency and reducing energy consumption.
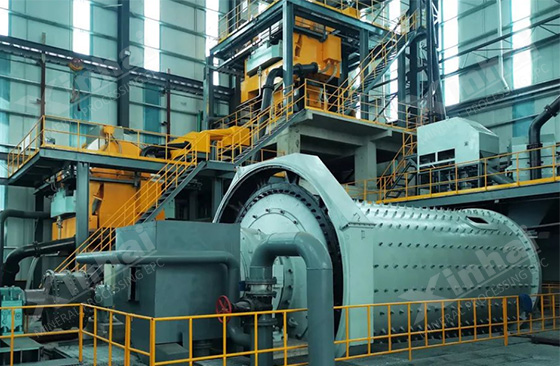
In the actual lithium ore beneficiation process, the particle size of the ore is usually adjusted through pre-treatment steps such as screening and classification to adapt to the requirements of the subsequent beneficiation process. Through these measures, the recovery rate and mineral processing efficiency of lithium ore can be maximized while reducing production costs and environmental impact.
02Lithium ore desliming treatment
Sludge is easily produced during the crushing process of lithium ore. Lithium ore desliming is an important step in the lithium ore processing process, and it has a significant impact on the separation effect. Desliming refers to the process of removing fine particles (slurry) from the slurry. These fine particles usually include clay minerals, fine-grained minerals and organic matter.
Lithium minerals in lithium ores, such as spodumene and lepidolite, are usually closely symbiotic with gangue minerals such as quartz and feldspar. These minerals tend to form fine particles, namely slime, during the crushing and grinding processes. At the same time, during the natural weathering process of lithium ore, a layer of fine-grained slime may form on the surface, and these slimes will be mixed into the ore slurry during the mineral processing process.
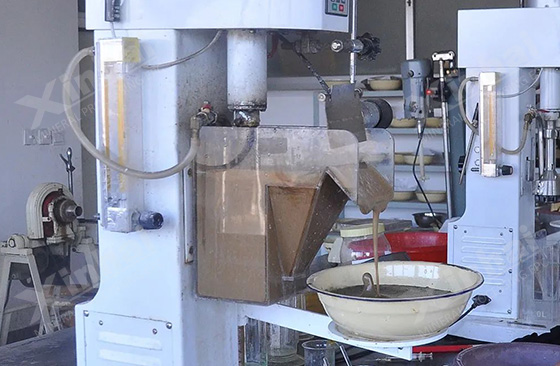
The impact of slime on lithium ore processing is mainly reflected in the following aspects. The presence of slime will reduce flotation efficiency because fine-grained minerals may cover the surface of lithium minerals, affecting the effective contact between the flotation agent and lithium minerals, thereby reducing the recovery rate of lithium minerals.
Sludge may affect the stability of the foam, making the foam layer thinner, which is not conducive to the floating and collection of lithium minerals. At the same time, in order to improve the dispersion of slime and suppress its negative impact on flotation, it may be necessary to increase the dosage of flotation reagents, which will increase production costs.
In order to reduce the negative impact of slime on lithium ore beneficiation, desliming operations are usually performed before mineral processing to reduce the impact of slime on the subsequent flotation process.
03Lithium ore processing water quality
The quality of mineral processing water plays a vital role in the lithium ore separation process. It directly affects the mineral processing efficiency, flotation effect, and the quality and recovery rate of the final product.
The pH value, hardness, temperature and dissolved ion species of water quality will all affect the activity and effect of flotation agents. For example, changes in pH value may change the charge state of the mineral surface, thereby affecting the adsorption capacity of the flotation agent and minerals. Water with higher hardness may introduce calcium, magnesium and other ions, which may compete with the flotation agent for adsorption sites and reduce the selectivity of the flotation agent.
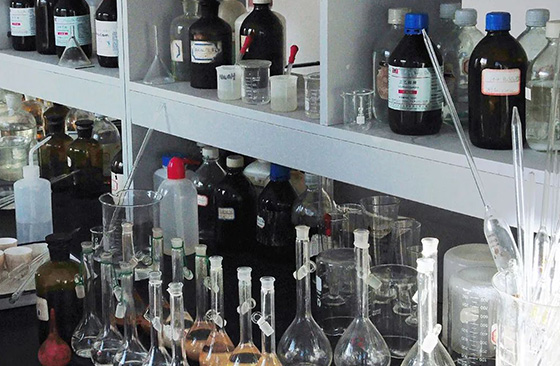
In addition, impurities in the water, such as oils, organic matter and surfactants, may affect foam stability. Unstable foam can result in mineral losses or reduced concentrate grade. In addition, the temperature of the water quality will also affect the formation and stability of foam. Certain ions in the water, such as copper, iron, lead and other heavy metal ions, may form complexes with the minerals in the lithium ore, changing the flotability of the minerals. This may reduce lithium mineral recovery or cause non-target minerals to be incorrectly flotated.
Therefore, in order to optimize the mineral processing process, improve the recovery rate and concentrate grade of lithium ore, and reduce production costs and environmental risks, the mineral processing water must be strictly controlled and adjusted, which usually includes using purification equipment to remove impurities in the water, or adding specific chemical reagents to improve water quality.
04Lithium ore flotation foam
The flotation foam layer of lithium ore is mainly composed of useful minerals in lithium ore. Due to their surface hydrophobicity, these minerals can interact with the flotation agent and adhere to the bubbles to form a foam layer. This selective aggregation enables the effective separation of lithium ore and gangue minerals. By optimizing the flotation process and foam management, the flotation efficiency of lithium ore can be effectively improved, ensuring the quality of the final product while reducing production costs and environmental risks.
The stability of the foam layer is crucial for the recovery of lithium ore. A stable foam layer helps the lithium ore particles float and collect, while unstable foam may lead to mineral loss or a decrease in concentrate grade. Its thickness needs to be properly controlled to ensure that the lithium ore particles can be effectively captured and floated. A foam layer that is too thick may cause coarse-grained lithium ore minerals to fall into the groove, while a foam layer that is too thin may cause gangue minerals to be entrained.
The chemical composition of the foam layer includes collectors, conditioners, mineral particles and possible impurities. The interaction of these components affects the properties of the foam layer, such as viscosity, elasticity and rupture, which in turn affects the flotation effect.
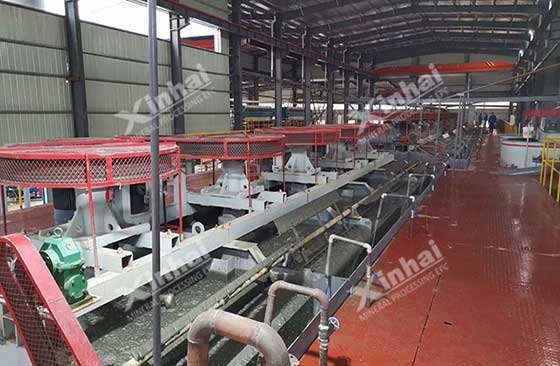
During the flotation process, it is necessary to optimize the formation and stability of the foam layer by adjusting flotation conditions (such as pH value, temperature, chemical system, etc.) to achieve the best lithium ore separation effect. After the foam layer is formed in the flotation tank, it needs to be effectively separated and collected. This process is usually accomplished with a foam scraper or foam tank. The separation efficiency of foam directly affects the recovery rate of lithium ore.
The above are the four key factors in lithium ore processing, which together determine the recovery rate of lithium ore and the quality of the concentrate. A professional mineral processing technology team is crucial to optimizing these key factors. They can ensure efficient separation and recovery of lithium ore, improve overall mineral processing efficiency, reduce costs and reduce environmental impact through precise process control, equipment debugging and pharmaceutical formula optimization. Today, with the increasing demand for new energy materials, having a professional mineral processing technology team plays an irreplaceable role in ensuring the efficient development and utilization of lithium resources.
05Part of Xinhai Mining Non-ferrous Metal Concentrator Project
1. Zimbabwe 5000TPD lithium ore dressing plant project
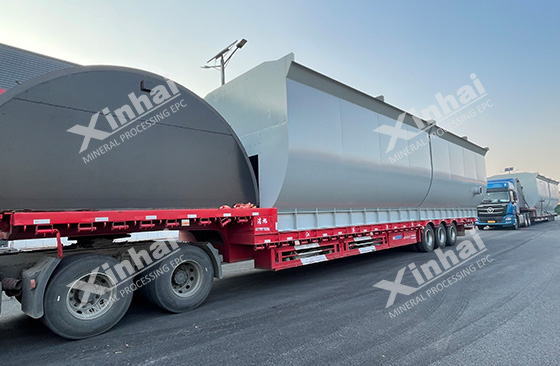
2. Yunnan 4400tpd copper ore dressing plant project
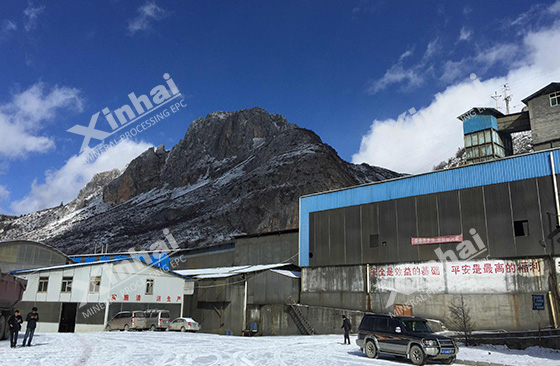
3. Shandong 2000tpd molybdenum ore dressing plant project
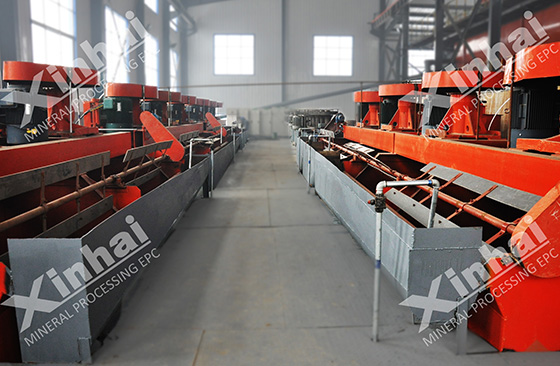
4. Pakistan 1500tpd copper ore dressing plant project
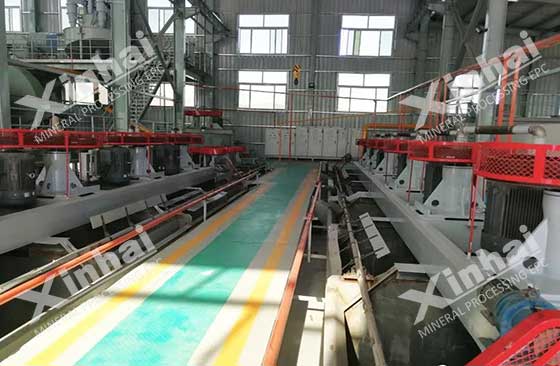
5. Mexico 1500tpd copper, lead, zinc, gold and silver multi-metal processing plant project
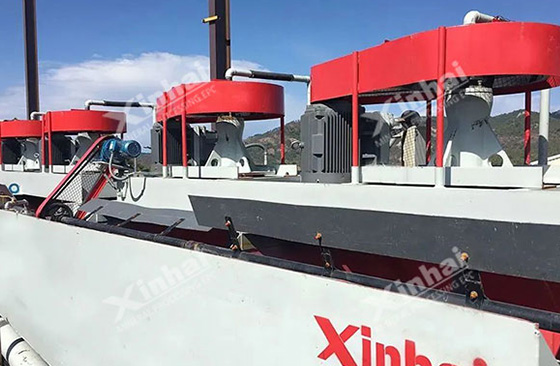
6. Nigeria 1000tpd copper and silver ore dressing plant project
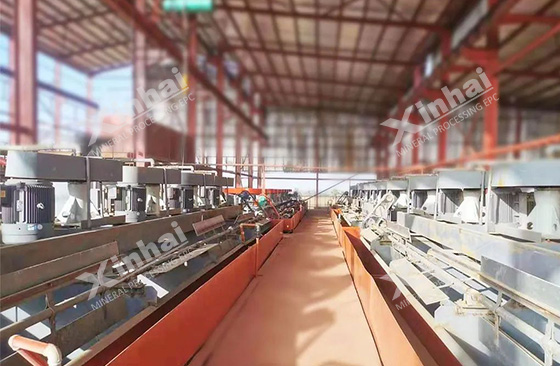