With the continuous exploitation of ore resources, its high-grade and high-quality ore resources are decreasing year by year. The industry is paying more and more attention to the development and utilization of refractory ores with low taste, fine particle size, polymetallic semi-raw, and complex structure. Copper oxide ore is one of the refractory ore resources. Due to the greater nature of copper ores in different regions, their overall degree of development and utilization is poor. At present, for the beneficiation of low-grade copper oxide ores, the main processes currently include flotation and combined beneficiation and smelting processes. The following will introduce the copper oxide mineral processing technology around these two parts.
Use the table of contents below to navigate through the guide:
01Flotation technology for copper oxide mineral processing
The flotation process is the main method for recovering copper oxide, including sulfide flotation, direct flotation with fatty acid collectors, flotation with amine collectors, etc. The fatty acid collector direct flotation method is used to treat copper oxide minerals such as malachite with simple gangue and high grade, and the amine collector flotation method is used to treat copper oxide ore containing lead-zinc ore.
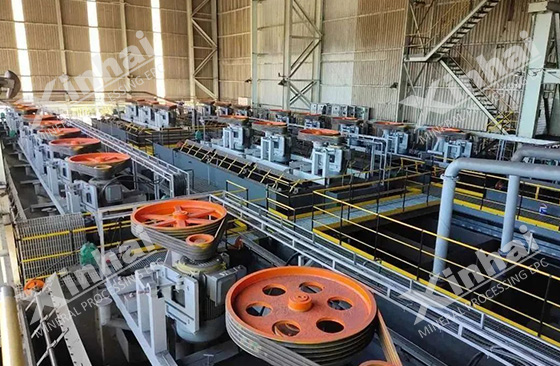
(1) Sulfide-xanthate flotation: This process can effectively flotate and recover basic carbonate minerals of copper such as malachite and azurite, and copper oxide minerals. Xanthate is a commonly used collector in copper oxide ore flotation. In addition to butyl xanthate, cyclohexyl, sec-butyl, isobutyl, etc. can replace n-butyl xanthate.
(2) Direct flotation with chelating collector: Organic chelating agents are used for flotation separation of non-sulfide ores. For copper oxide minerals, including chrysocolla, hydroxamic acid can be used as a collector to effectively recover copper minerals.
(3) Sulfidation-combined drug flotation: Copper oxide can achieve good beneficiation indicators by using sulfide-combined drug flotation. During flotation, a vulcanizing agent is first added to the slurry for vulcanization, and then dixanthate + hydroxamic acid + kerosene are added. The combined collector and enhanced collector can improve the recovery rate of copper concentrate.
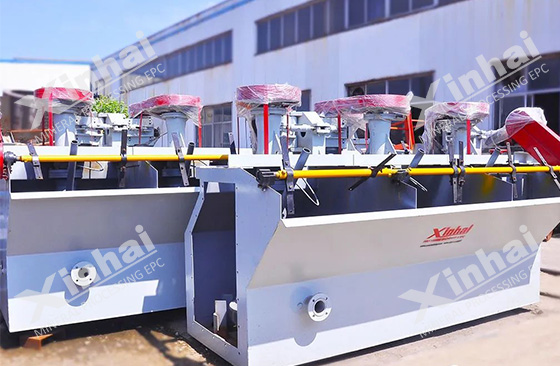
Although copper oxide flotation recovery is widely used in mineral processing plants, there are still many problems in actual production, such as the problem of sludge. Sludge will have many adverse effects on copper oxide sulfide flotation, and may even make flotation difficult. In order to eliminate the influence of sludge, the ore feeding part can be fully washed and polymers can be added to the flotation slurry. Methods such as flocculant and dispersant are added to disperse the slime. The copper oxide flotation recovery process should strengthen and select new flotation reagents and formulate a reasonable process flow based on the properties of copper oxide.
02Combined technology for copper oxide mineral processing
The comprehensive utilization level of copper oxide ore can be improved by using a combination of dressing and smelting process or chemical beneficiation method. The main methods include leaching-extraction-electrowinning method and acid leaching or alkali leaching after roasting pretreatment.
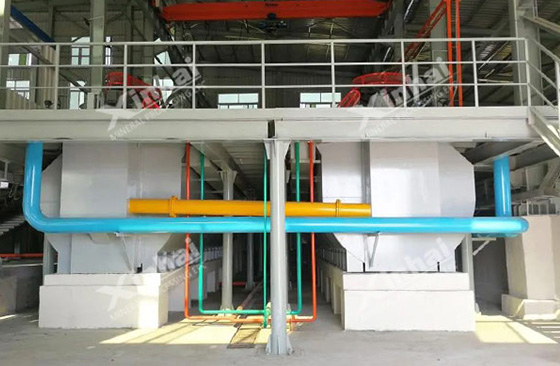
(1) Leaching-extraction-electrowinning: This process has been widely used due to its advantages of low investment, simple process flow, low cost of electrolytic copper, and full utilization of secondary resources. At present, the main production methods of wet copper are heap leaching and stirring leaching. Which leaching method to choose should be determined according to the actual situation of the mineral processing plant. The copper ore is granulated and heap leached, and then the extraction-electrodeposition process is used to produce electric copper. The concentration of copper in the leach solution increases, and the leaching rate also increases. When acid leaching, extraction, click, replacement and other methods are combined to treat copper oxide, high-purity copper products can be obtained.
(2) Other combined dressing and smelting technologies: Methods used to treat low-grade copper oxide ores include roasting pretreatment, microwave irradiation, acid leaching-sulfidation precipitation-flotation, isolation-flotation, underground leaching, and hydrothermal sulfidation. -Flotation, etc. Among them, the acid leaching-sulfide precipitation flotation process can further improve the recovery rate of copper ore compared with the conventional sulfide flotation process. This type of process has also been applied in actual production.
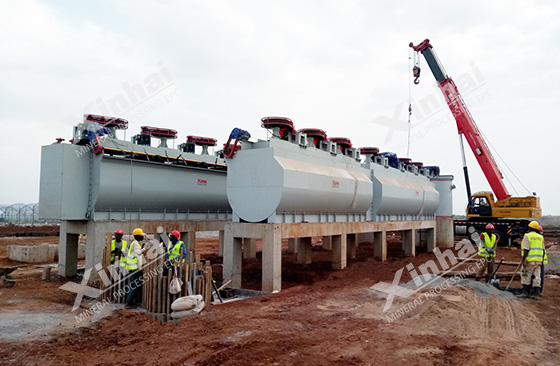
The above content is a brief introduction to the mineral processing technology of low-grade copper oxide ore. In actual production, appropriate adjustments will be made according to the properties of the ore and production requirements. At present, as the taste of mined copper ore continues to decline and the amount of difficult-to-process copper ore continues to increase, it is necessary to continuously improve the level of copper ore beneficiation technology and equipment. When the mineral processing plant selects the mineral processing technology and equipment for copper ore, it should be based on the mineral processing test results. Based on the test results, a reasonable mineral processing technology solution and equipment configuration can be obtained to improve the overall production efficiency.