Tungsten is a refractory metal with a melting point as high as 3410±20°C. It is the metal with the highest melting point and has high-temperature strength and hardness. The vapor pressure is still very low at high temperatures of 2000~2500℃. Tungsten is used in industries such as steel, machinery, mining, petroleum, rockets, aerospace, electronics, nuclear energy, military industry and light industry in the form of alloy elements, tungsten carbide, metal materials or compounds. It is indispensable to various sectors of the national economy and cutting-edge technology. Important material. There are twenty kinds of tungsten minerals discovered in nature, among which the two types with industrial value are wolframite and scheelite. The mineral processing method and process flow should be selected according to the specific type of ore. The main mineral processing methods of wolframite ore are briefly described here.
Use the table of contents below to navigate through the guide:
01Wolframite ore pre-enrichment
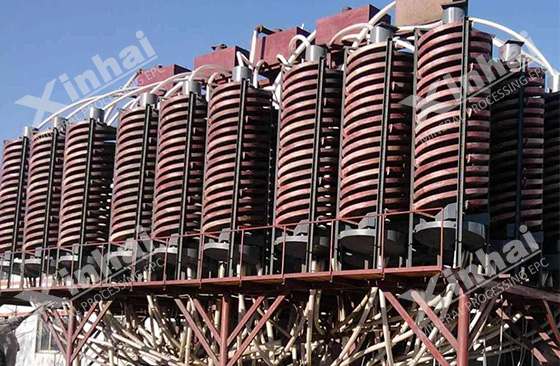
Most mining of wolframite ores has a high dilution rate, generally exceeding 80%, so coarse and poor waste rocks need to be discarded in advance before gravity separation. Since the boundary between the ore-bearing gangue and the surrounding rock is clear and distinct in color, it is easy to identify. After grading the ore tin ore, manual hand selection can be used to discard a large amount of waste rock. In particular, hand selection of coarse-grained ores can improve production efficiency. Hand selection is often combined with other methods (heavy media beneficiation, photoelectric sorting, etc.) to pre-enrich wolframite ore to improve concentrate recovery and waste rock disposal rates.
02Wolframite ore gravity separation process
Gravity separation is the main beneficiation method of wolframite ore. Wolframite has a high density, and gravity separation technology can effectively separate it from minerals with a density less than 3.5-4. For wolframite in quartz vein wolframite deposits, because of its large crystal grains, it is more suitable to recover it by gravity separation in the case of coarse grains. Gravity equipment such as shakers and jigs are often used in gravity selection operations. Jig machines are used for coarse and medium-grained wolframite ores, while shakers are used for medium- and fine-grained minerals.
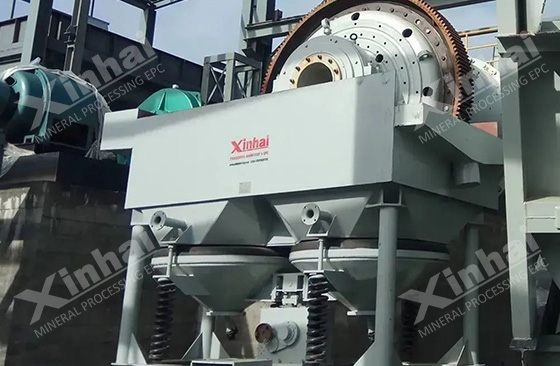
Using jigging: the ore is screened into three levels before selection, and then classified into the jig machine. In order to reduce the sludge phenomenon of wolframite ore, jig equipment is installed in the grinding cycle operation to recover the dissociated tungsten mineral as soon as possible.
Using a shaking table: When using a shaking table to reselect fine-grained ores, the enrichment ratio of minerals can be increased. In order to improve the re-selection effect, strict classification is required before entering the shaker.
Use spiral concentrator: Spiral concentrator has large processing capacity and low cost. It is more suitable for processing slightly coarser materials, especially for selecting poor materials.
03Wolframite ore fine mud treatment
Due to the brittleness of tungsten ore, sludge is prone to occur during the mineral processing process. There are three main sources: ore washing water before pre-selection, dehydration during gravity separation operations, and overflow water from the classifier. Before selection, these overflow waters need to be concentrated, concentrated, and then treated separately. Commonly used equipment include shakers, centrifugal concentrators and chutes. Among them, the centrifugal concentrator has a large processing capacity and a high recovery rate. It is an efficient roughing equipment.
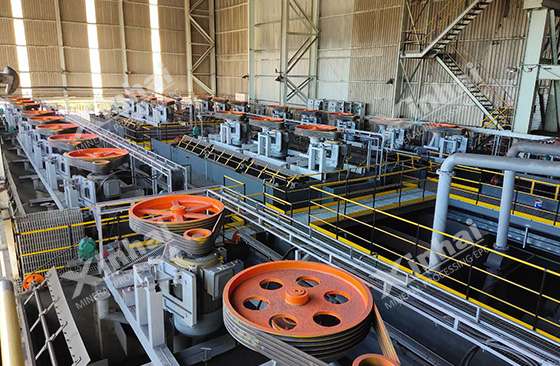
When flotating the fine mud of wolframite ore, collectors such as styrenephosphonic acid and alkyl hydroxamic acid can be used. Lead nitrate and ferrous sulfate can be used as activators for wolframite flotation. New technologies such as branched series flow flotation, fractional speed selection, and thick slurry aeration and stirring can save flotation chemicals and improve flotation effects.
In addition to conventional flotation methods, carrier flotation, hydrophobic agglomeration, magnetic separation, etc. can also be used. These methods can be used to improve the separation effect of black tungsten fine mud.
04Wolframite ore concentrate enrichment
In the gravity separation process, in addition to wolframite, minerals with higher density such as cassiterite, scheelite and most sulfide ores will enter the coarse concentrate together with wolframite. Therefore, a selection process must be set up to increase the tungsten content. The grade of the concentrate.
Commercial tungsten concentrate can be obtained after table flotation and flotation separate sulfide ore from gravity separation coarse concentrate. Table flotation floats out sulfide ore in a coarse-grained condition, and removes part of the gangue mixed in during the production process, further improving the grade of tungsten concentrate. Table float, as an efficient selection equipment, has been widely used in tungsten selection operations. Qualified tungsten concentrate can be obtained from coarse concentrates with low tin content through Taiwan Floatation Concentration. Table Floatation can also be used to separate scheelite and cassiterite.
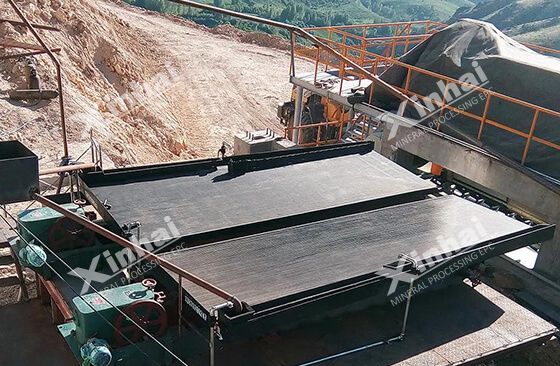
Magnetic separation can be used to separate wolframite from cassiterite and scheelite. Electric separation is mainly used for the separation of scheelite and cassiterite. Electric separation can be used to process tungsten concentrate containing xenotime, separate the xenotime, and reduce the phosphorus content in the wolframite concentrate.
The above is a brief description of the wolframite ore beneficiation process. Formulating a specific beneficiation process based on the characteristics of the ore can improve the efficiency of the production line while reducing production costs. Xinhai Mining relies on years of experience in EPC+M+O service to customize wolframite ore beneficiation processes and equipment for you.