There are different types of iron ore in nature, mainly divided into magnetite, hematite, limonite, siderite, ilmenite and chromite. The beneficiation methods adopted by different types of ores are of course quite different. The following will introduce you to the different beneficiation technologies of the above three iron ores.
Use the table of contents below to navigate through the guide:
01Siderite Mineral Processing Technology
As a widely distributed mineral, the composition of siderite is ferrous carbonate. When a large amount of siderite is gathered and the content of harmful impurities is low, it can be used as iron ore. Its beneficiation technology is divided into three categories: magnetization roasting technology, strong magnetic separation technology, flotation technology.
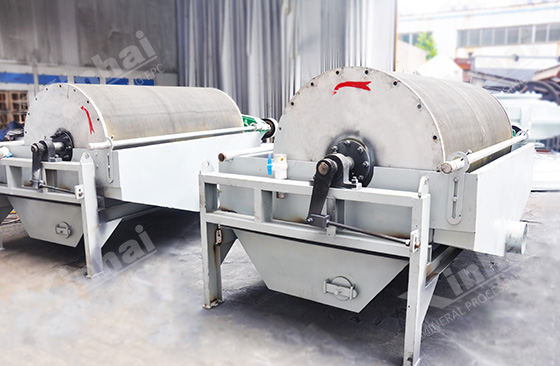
Magnetization roasting technology: After the ore is heated to a certain temperature, it undergoes a physical and chemical reaction, and the siderite is thermally decomposed and converted into strong magnetic magnetite and maghemite. There are several types of magnetization roasting, such as piled state magnetization roasting and fluidized magnetization roasting. When magnetizing siderite roasting, the main attention should be paid to the cooling method.
Strong magnetic separation technology: Because (magnesium) siderite has weak magnetism, strong magnetic separation technology can separate weak magnetic minerals including (magnesium) siderite.
Flotation technology: The flotation of siderite is mainly divided into two types: forward flotation to enrich iron and reverse flotation to desiliconize.
02Ilmenite Mineral Processing Technology
Ilmenite is a weakly magnetic mineral and often coexists with magnetite and vanadium-titanium magnetite. The beneficiation methods are mainly gravity separation, electric separation, magnetic separation, flotation and combined beneficiation.
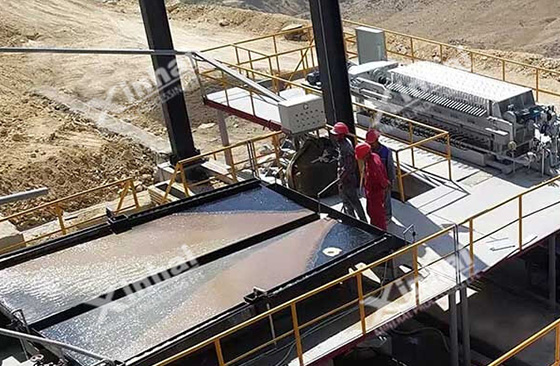
Gravity separation method: The density of ilmenite is higher than that of gangue minerals, and gravity separation is used as pretreatment or rough separation is used to throw tails. The gravity separation method has the characteristics of low production cost and less environmental pollution. Shakers are generally used as equipment for beneficiation and re-election of ilmenite, and are widely used in small mines.
Electric separation method: When the ore contains ilmenite, rutile, zircon and other minerals, electric separation can be selected. Electric separation is widely used in beneficiation plants as the gate operation of titanium concentrate production.
Magnetic separation: Magnetic separation is used in the beneficiation of titanium-containing minerals, mainly divided into weak magnetic separation and strong magnetic separation.
① Weak magnetic separation can separate out the titano-magnetite remaining in the tailings, which is helpful for the smooth operation of strong magnetic separation.
② Strong magnetic separation can remove qualified tailings, improve the grade of titanium flotation, and reduce the amount of ore in titanium flotation.
③ High-gradient magnetic separation can recover the fine-grained ilmenite in the ore, and part of the fine mud in the ore can also be thrown away to complete the rough separation and tailing of the original ore.
Flotation method: Flotation method is an effective method for recovering fine-grained ilmenite, which is mainly used for beneficiation of primary titanium ore, especially fine-grained titanium-containing ore, and sometimes also for the beneficiation of rough concentrate.
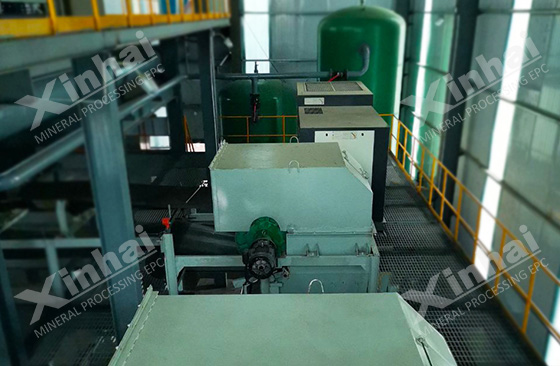
Combined beneficiation method: The combined beneficiation method of ilmenite includes gravity separation-flotation, gravity separation-electric separation, magnetic separation-flotation, magnetic separation-gravity separation-flotation, etc. First add dispersant to the pulp, and then re-throw strong magnetic minerals in a medium magnetic field. The processes of strong magnetic roughing and electric separation can further improve the concentrate grade and recovery rate. At the same time, strong magnetic separation-flotation is a better method for processing fine-grained ilmenite.
03Chromite Mineral Processing Technology
Because chromite is a lean ore, it must be beneficiated. Most of the chromite ore is fine-grained or fine-grained and associated with beneficial metals such as high-phosphorus ore and high-iron ore, which brings certain difficulties to beneficiation. The beneficiation of chromite is generally divided into ore washing, gravity separation, strong magnetic separation, gravity separation-magnetic separation and other processes.
Chromite ore washing operation: ore washing mainly uses hydraulic or mechanical force to separate ore and mud. The ore dressing plant can use ore washing screen, cylinder washing machine or trough washing machine for ore washing. Washing operations are often accompanied by screening processes. Chromite can be directly washed with water on the vibrating screen, or the clean sand obtained from the washing machine can be sent to the vibrating screen for screening.
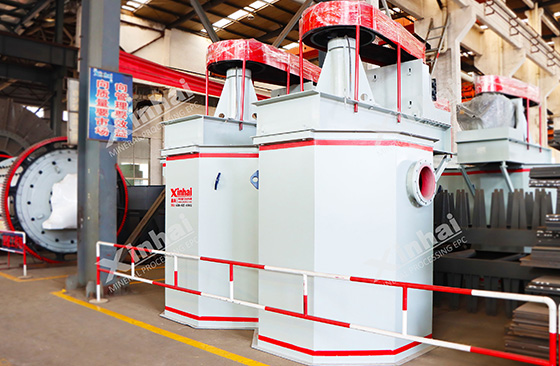
Chromite ore gravity separation operation: If the chromite ore structure is simple, the embedded particle size is relatively coarse, or the chromium oxide ore with high density is selected, gravity separation operation can be used. Dense media beneficiation, jigging beneficiation and shaking table beneficiation are commonly used gravity beneficiation methods.
Chromite strong magnetic separation operation: Since chromium minerals are weak magnetic minerals, the grade of chromium will be improved when using strong magnetic separator for ore separation.
Chromite gravity separation-magnetic separation operation: This method is mainly used to process leached chromium oxide ore. The clean sand is first treated with a jig and then sorted with a magnetic separator.
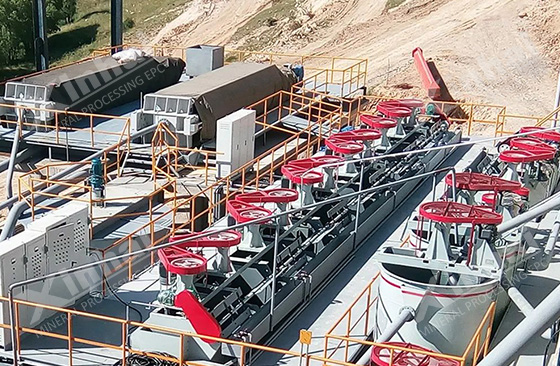
The above is a brief description of several different iron ore beneficiation technologies. In actual production, the beneficiation plant will improve and adjust the beneficiation process according to the characteristics of the ore itself, in order to obtain a higher concentrate recovery rate. Therefore, Xinhai Mining recommends to conduct a beneficiation test analysis on the raw ore before determining the beneficiation process. The test result has an important basis for the design of the subsequent beneficiation process. Xinhai Mining can provide you with accurate iron ore beneficiation tests, customized iron ore beneficiation schemes, and efficient iron ore beneficiation equipment. If necessary, please leave a message for consultation.