The continuous development of global industry and agriculture has led to the annual consumption of phosphate ore resources. High-grade phosphate resources are gradually decreasing. Therefore, it is very important to increase the development and utilization of medium and low-grade phosphate resources to meet the needs of industry and life. This part of the phosphate resources cannot be directly processed by scrubbing and desludging technology, but generally needs to be used after mineral processing and enrichment. Medium and low-grade phosphate resources are often enriched by flotation technology, that is to say, strengthening the application of flotation technology in the phosphate resource beneficiation industry can improve the utilization rate of this part of mineral resources. The flotation effect is mainly determined by the interaction between mineral particles and bubbles in the water medium. Factors such as flotation reagent system, operating conditions, and equipment performance will affect the effect of the interaction between mineral particles and bubbles. Common phosphate ore flotation processes mainly include positive flotation process, reverse flotation process, positive-reverse flotation process, reverse-positive flotation process, and double flotation process. The following will introduce the characteristics of these flotation processes and reagent characteristics.
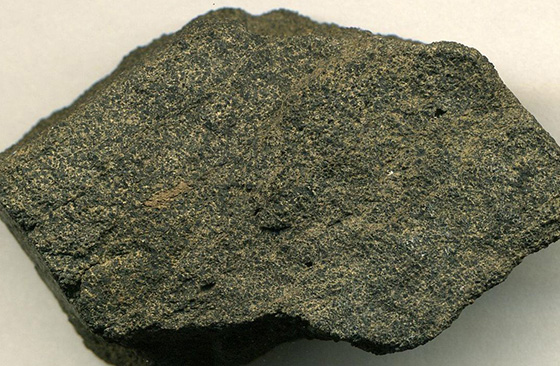
Use the table of contents below to navigate through the guide:
01Phosphate ore direct flotation process
After grinding, the phosphate ore reaches the degree of monomer dissociation. After adding water to a certain concentration in the pulp, a collector is added to enrich the phosphate minerals in the foam product. During flotation, inhibitors are added to the pulp to inhibit the floating of gangue minerals such as silicates and carbonates.
Process characteristics:
(1) For medium and low-grade phosphate ores, especially those with a magnesium oxide mass fraction of less than 2%, the mass fraction of magnesium oxide in the concentrate can be controlled to a value less than 1 by direct direct flotation. There is no need to use a two-stage flotation process, which simplifies the mineral processing process and reduces gangue minerals.
(2) For low-grade high-magnesium oxide phosphate ores, direct direct flotation and reverse flotation can be used to ensure the quality of the final phosphate concentrate.
(3) The direct direct flotation process can effectively reduce the mass fraction of iron and aluminum impurities in the ore, so the impurity removal effect of this process is obvious.
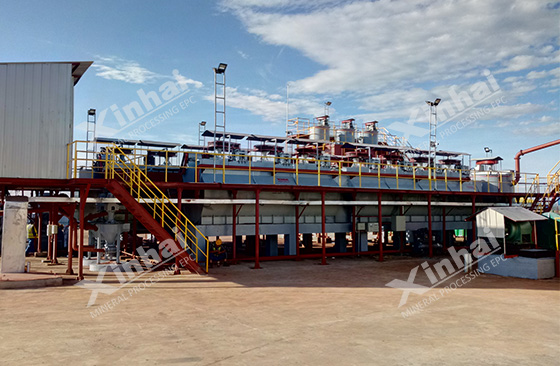
02Phosphate ore reverse flotation process
The reverse flotation process is mainly used to separate phosphate minerals from dolomite gangue minerals. Before flotation, inorganic acid is used to adjust the pH value of the pulp to weak acidity, and then a specific collector is added to enrich the dolomite in the foam product, while the phosphate concentrate remains in the tank. The reverse flotation process can increase the discharge rate of dolomite gangue minerals to 70%-80%.
Reverse flotation process reagent characteristics:
The types of reverse flotation collectors are mainly modified fatty acid collectors, cationic collectors and mixed collectors. After sulfation modification or saponification, the water solubility, temperature resistance, capture and selectivity of fatty acids can be further improved. Cationic collectors dissociate and produce amines with hydrophobic hydrocarbon groups when acting, which are mainly used to capture aluminum silicate ores such as quartz, feldspar and non-ferrous metal oxide ores. Mixed collectors are a combination of fatty acids and their derivatives or other reagents.
Process advantages:
(1) The reverse flotation process can achieve low room temperature flotation and simplify the process. Save energy.
(2) The coarse particle size of the tank product obtained by reverse flotation is conducive to the subsequent thickening of the product.
(3) The reverse flotation process complies with the flotation process principle of "floating less and suppressing more".
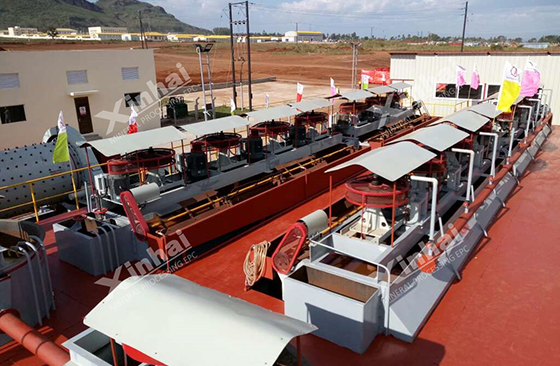
03Phosphate ore direct-reverse flotation process
The direct-reverse flotation process is mainly used to process siliceous-calcium phosphate ore. Inorganic alkali is added to the pulp to adjust it to weak alkalinity. The phosphate minerals are enriched in the foam product by the collector, and the silicate gangue minerals remain in the flotation tank. Inorganic acid is added to adjust the pulp to weak acidity. The direct flotation concentrate uses the collector to enrich carbonate impurities, and the useful mineral phosphate minerals remain in the flotation tank. The purpose of reverse flotation is to remove magnesium oxide impurities in the concentrate.
Process characteristics:
(1) This process has strong adaptability to the quality of the original ore.
(2) The phosphate concentrate obtained by reverse flotation has a coarse particle size, and it is easy to produce a foam product after dehydration, which is convenient for sedimentation and transportation.
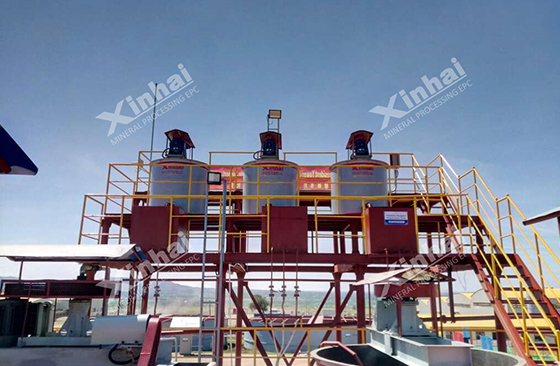
02Phosphate ore reverse flotation process
The process sequence is opposite to the above-mentioned forward and reverse flotation process. Now the carbonate gangue minerals are floated out under acidic medium to obtain reverse flotation concentrate, and then the reverse flotation concentrate is subjected to secondary grinding to dissociate the siliceous gangue minerals, and the phosphate minerals are floated out under alkaline conditions to obtain the forward flotation concentrate. After the secondary grinding, the ore surface is refreshed, which is conducive to the separation of silicon and phosphorus. The characteristics of this process are similar to those of the forward and reverse flotation process, with strong adaptability to the original ore and ideal concentrate indicators. The consumption of inorganic acid in the flotation process is small, but the consumption of alkaline materials increases. When phosphoric acid is used as an inhibitor, the cost of reagents can be reduced.
05Phosphate ore double reverse flotation process
The separation of phosphate minerals from dolomite and quartz gangue minerals mainly adopts double flotation process. In the double flotation process, fatty acid collectors are generally used to enrich dolomite gangue minerals and foam in weakly acidic slurry, and then fatty acid collectors are used to enrich quartz gangue minerals. Finally, useful minerals remain in the flotation tank.
Process characteristics:
(1) The double flotation process can be carried out at low room temperature or at a coarse particle size, which simplifies the mineral processing process and reduces energy consumption.
(2) The phosphate concentrate obtained by double flotation has a coarse particle size, which is conducive to the treatment of subsequent products.
(3) The wastewater generated during the double flotation process is acidic and can be recycled as return water.
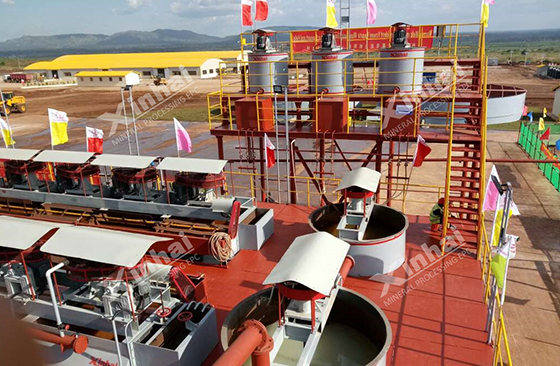
The above contents are several common flotation processes and process characteristics of phosphate ore. The flotation process technology of phosphate ore needs to be determined according to the requirements of phosphate concentrate indicators and the differences in the properties of the original ore. Single flotation operation is suitable for phosphate ore with phosphate or silicate as gangue minerals. Positive flotation requires heating of the slurry, while the reverse flotation process can be carried out at room temperature, mainly due to the different performance of the flotation reagents. The combined flotation process can process phosphate ore containing both quartz silicates and dolomite carbonates, with fine embedded particle size. The positive and reverse flotation processes can process most of the difficult-to-process medium and low-grade phosphate ores, and the product indicators are relatively stable.