As an important industrial metal, molybdenum is widely used in metallurgy, chemical industry, machinery manufacturing and other fields. The development and utilization of molybdenum mineral resources has a positive role in promoting national economic development. In order to utilize molybdenum ore resources more efficiently, it is crucial to select appropriate mineral processing technology and equipment. This article will introduce you to conventional and refractory molybdenum ore beneficiation processes to help you utilize molybdenum mineral resources more efficiently.
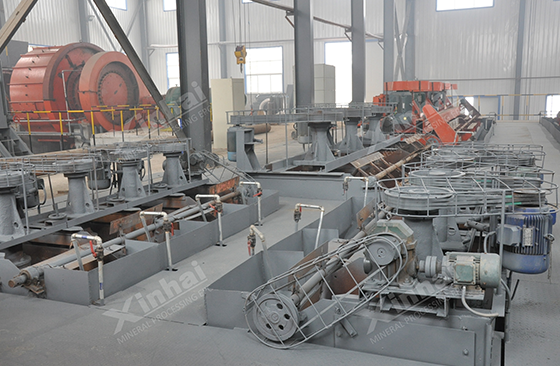
Use the table of contents below to navigate through the guide:
01Commonly used molybdenum ore beneficiation processes
The molybdenum ore concentrator mainly uses flotation method, and the target mineral recovered is molybdenite. Molybdenite has good natural floatability due to its structure. When the ore is over-ground, the floatability of molybdenite decreases. Adding a certain amount of xanthate polar collector is beneficial to the recovery of molybdenite. The secondary mud produced by over-grinding will affect the flotation of molybdenum ore. Over-grinding should be avoided and prevented as much as possible before flotation. Generally, molybdenum mineral beneficiation plants will choose segmented grinding processes and multi-stage separation processes to gradually achieve single extraction and dissociation of minerals, thus ensuring the recovery rate of molybdenum concentrates.
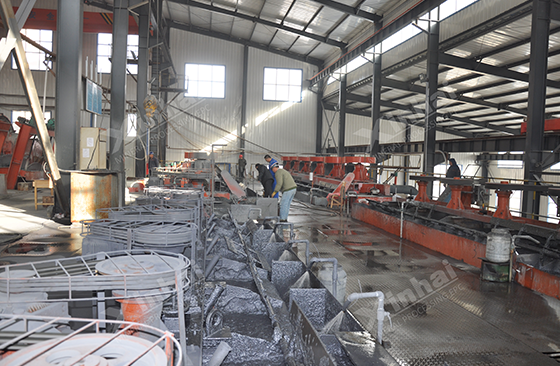
02Molybdenum ore beneficiation process
The molybdenum ore crushing process adopts a three-stage and one closed-circuit process. The grinding process adopts ball mill, rod mill + ball mill or semi-autogenous grinding process. The flotation process of molybdenum ore generally involves roughing to produce coarse concentrate, and the tailings are roughly swept to recover associated minerals or discarded directly. Molybdenum ore rough concentrate undergoes two to three stages of regrinding process and five to six times of beneficiation to obtain molybdenum concentrate.
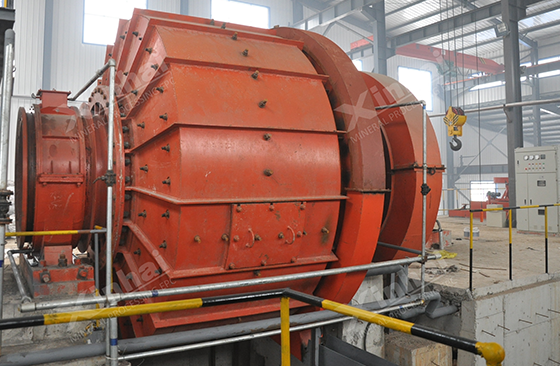
03Molybdenum ore beneficiation equipment
Flot ation columns are widely used in molybdenum ore concentrators because of their simple structure, high efficiency and energy saving, significant flotation effect on fine particles, simple flotation process, and convenient control of foam layer thickness, bubble size, and number of bubbles. After the molybdenum ore coarse concentrate enters the beneficiation stage, it needs to be ground again. The finer particle size can increase the enrichment ratio, and then the flotation column is used for beneficiation. The good environment of dynamic collision between bubbles and ore particles and static separation of bubble particle combinations in the flotation column is conducive to the separation of fine or micro-grained molybdenum ore, and the number of selection times is greatly reduced. In addition, flotation columns are easy to realize automatic control and are suitable for molybdenum ore beneficiation. Therefore, flotation columns are widely used in molybdenum ore and copper-molybdenum ore beneficiation plants.
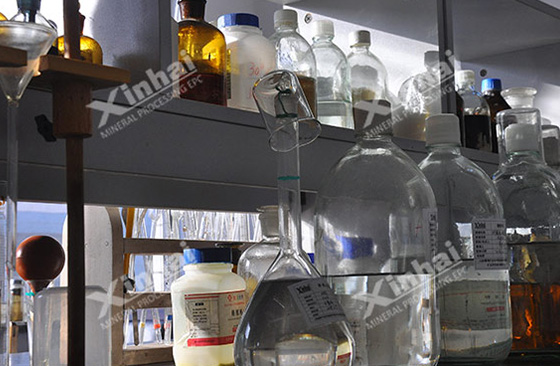
04Molybdenum ore beneficiation agent
During the flotation of molybdenum ore, non-polar oil is often used as a collector. A frother is added during flotation. Lime is used to adjust the pH value of the slurry, and water glass is used as an inhibitor of gangue minerals. In order to ensure the quality of molybdenum concentrate, minerals containing copper, lead, iron and other metals need to be separated during flotation. Drugs that inhibit the flotation of copper and iron include sodium sulfide or sodium hydrosulfide, cyanide or ferricyanide. The lead leaching agent uses chromate.
05Beneficiation process of refractory molybdenum ore
Separation of molybdenum ore containing calcium oxide and carbonaceous minerals
Gangue containing calcium oxide is easy to muddy, so be careful not to over-grind molybdenum ores containing such gangue minerals. In mineral processing practice, water glass, sodium hexametaphosphate or organic colloid are used as inhibitors for gangue minerals.
Although the floatability of carbonaceous minerals is similar to molybdenite, its density is smaller, so gravity separation can be used to remove it. Sodium hexametaphosphate and CMC can be used to suppress carbon and floating molybdenum. To suppress carbon, you can also use the chemicals ferric chloride, water glass and sodium hexametaphosphate. Roasting to remove organic carbon is also one of the methods.
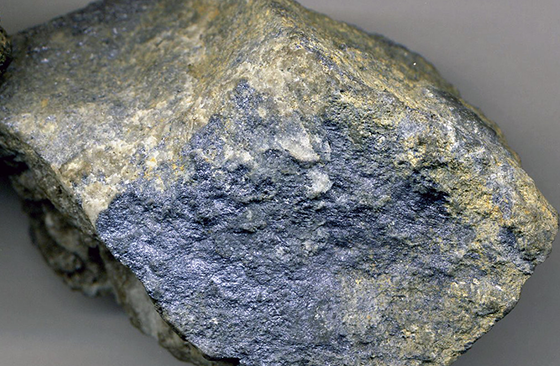
Talc and molybdenite separation
Talc is a common silicate mineral that is naturally floatable. It is an "equal flotatable mineral" with molybdenite, and the two are more difficult to sort. When sorting molybdenum concentrate from molybdenum ore containing 5%-10% talc, the recovery rate is very low. First use inhibitors to suppress talc, and use traditional collectors and frothers to float molybdenite. Talc inhibitors are mixtures of soluble weakly alkaline metal salts and strong acidic metal salts, such as mixtures of sodium silicate, sodium carbonate, etc. with zinc sulfate, aluminum sulfate, etc. The inhibitor is added by first adding the mixture of sodium silicate and zinc sulfate, After stirring with the slurry for 10-30 minutes, add a certain amount of sodium carbonate and stir, and then float molybdenite.
Separation of high oxidation rate molybdenum ores
After long-term wind erosion, rain, and sunshine, the upper part of the molybdenite deposit is partially oxidized, and part or most of the molybdenum sulfide is oxidized into molybdenum oxide or molybdenum ore. Molybdenum oxide minerals are natural hydrophilic minerals with many types of minerals. The surface physical and chemical properties of various molybdenum oxide minerals vary greatly. The mineral dissipation particle size is fine. It is a difficult-to-select molybdenum mineral. For example, molybdenum calcium ore and molybdenum iron ore can be absorbed by water. It is inhibited by gangue inhibitors such as glass and is significantly inhibited by gangue inhibitors such as quartz during flotation, while molybdenum is relatively easy to float.
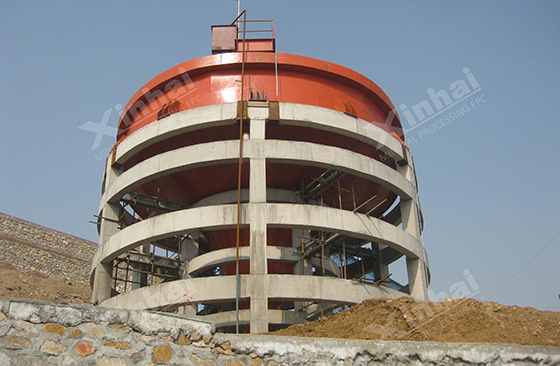
The selection of conventional and refractory molybdenum ore beneficiation processes needs to take into account various factors such as ore properties, mineral composition, and process technology. Only through continuous in-depth research and innovation, combined with modern scientific and technological means, can we better solve the problems in the molybdenum ore beneficiation process, improve the beneficiation efficiency, and achieve effective utilization of resources and sustainable development.