Phosphate ore is one of the most important mineral resources in the world. It is widely used in many fields such as phosphorus fertilizer, chemical industry, metallurgy, food, etc. With the gradual reduction of high-grade phosphate resources, developing low-grade, difficult-to-select phosphate mine has become a new direction of resource utilization.
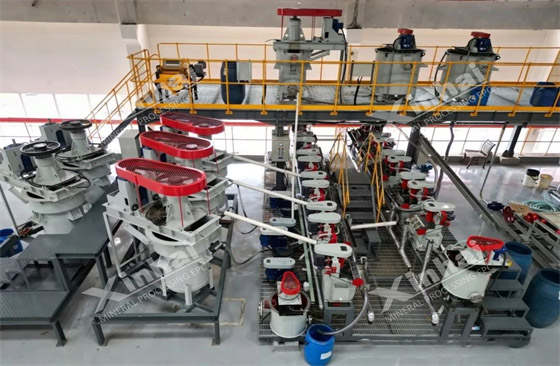
Gum phosphate ore is a typical difficult-to-select phosphorus ore, with high mud content, mineral-embedded fine, poor selectivity, and other characteristics; the beneficiation technology puts forward higher requirements. Recently, Xinhai Mineral Equipment carried out a pilot test of expanding continuous beneficiation and optimized the flotation process to realize the efficient separation and utilization of phosphorus resources around a gum phosphorus ore project.
Use the table of contents below to navigate through the guide:
01Ore properties
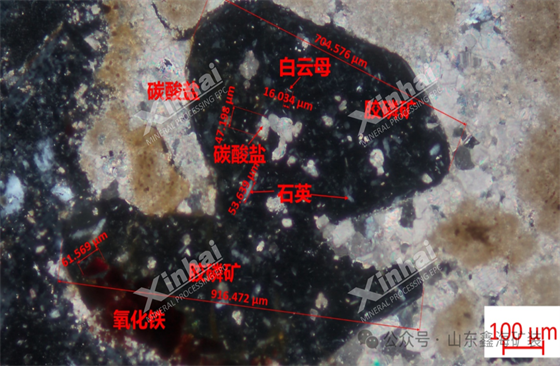
The main ore mineral in the raw ore is calcium phosphate. In contrast, the gangue minerals include carbonate minerals, quartz (SiO₂), mica, etc. The content of metal minerals is relatively low, with iron oxide minerals such as hematite being predominant, along with a small amount of pyrite. The primary valuable element in the raw ore is phosphorus. The grade of P₂O₅ is 24.83%, SiO₂ is 11.85%, MgO is 4.56%, and CaO is 42.51%. The main harmful impurities are SiO₂ and MgO.
02Expanded Continuous Beneficiation Pilot Test
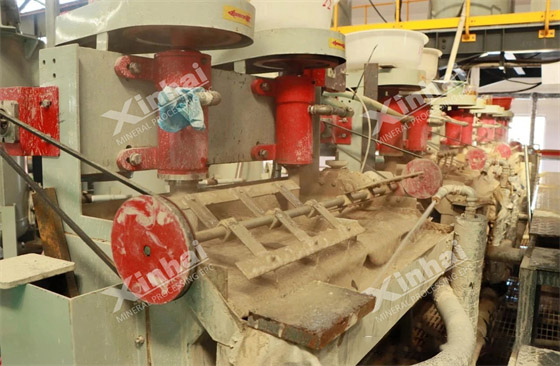
The process flow used in this pilot test is primarily based on the flotation process flow determined in the laboratory flow test. It has been improved and adjusted according to the specific conditions of the nature of the ore and the influence of the return of the ore in the debugging stage of the continuous flotation test on the effect of separation. The conditions of the chemicals are the average value of the test data of the actual amount of the substances. To ensure the flotation effect, the direct flotation operation was adjusted from one roughing, one scavenging, and one fine to two roughings, two scavengings, and two fines. The reverse flotation operation has not been adjusted. Through this joint flotation process, we strive to effectively separate collophane and veinstone minerals under the conditions of complex ore properties.
03Innovative process link
Crushing operation: The raw ore is crushed by a vortex machine, and the particle size after crushing is about -5 mm.
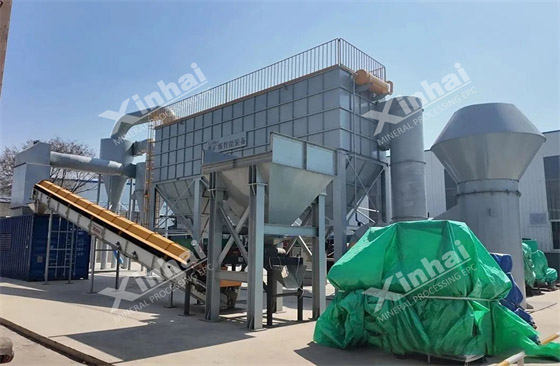
Grinding operation: The crushed ore is ground to 90% passing 200 mesh by a ball mill, which minimizes the occurrence of overgrinding.
Flotation: After a direct flotation process consisting of two roughings, two scavengings, and two cleanings, the obtained rough concentrate undergoes acid treatment followed by three-stage reverse flotation.
Concentration control: Due to the low concentration of the milled and graded products due to the finer grinding fineness, Xinhai uses a thickener to concentrate the qualified products to reach the appropriate concentration before entering the mixing tank, which effectively guarantees the effect of sorting.
Reagent system: In the stage of extended continuous pilot test, Xinhai Mining Research Institute team dynamically optimizes the reagent formulation based on the laboratory program, combined with the on-site flotation phenomenon, to enhance the ore-carrying capacity of direct flotation foam, and effectively remove SiO₂ and MgO in the reverse flotation stage. after several rounds of adjustment during the commissioning phase, the average of the results of each dosage test during the continuous operation of flotation is taken as the final dosage of the reagent.
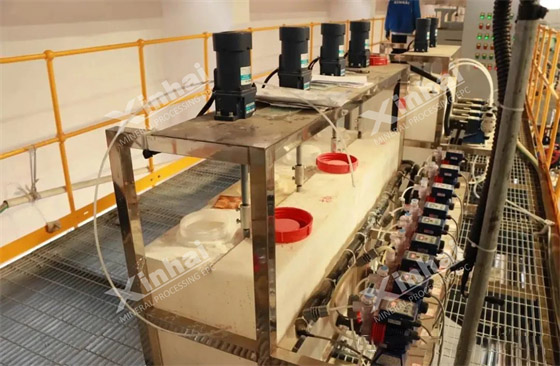
Flotation time: the number of flotation tanks used was calculated based on the laboratory flow test and the specifications and capacity of the flotation machine used, and then adjusted appropriately according to the return of the ore in the extended continuous test and the actual situation.
Temperature control: The test was carried out in Yantai during winter. In response to the low-temperature problem, the Xinhai Mining Research Institute team set up additional heating devices to prepare chemicals and the flotation process. It stabilized the temperature of the slurry at about 28℃ to ensure the reagent performance, flotation efficiency, and the recovery of phosphorus cleanings.
Continuous test: The extended continuous test runs continuously and stably for 72 hours, with a processing capacity of 120kg/h. It verifies the process's industrialization feasibility, and the data accuracy far exceeds the laboratory.
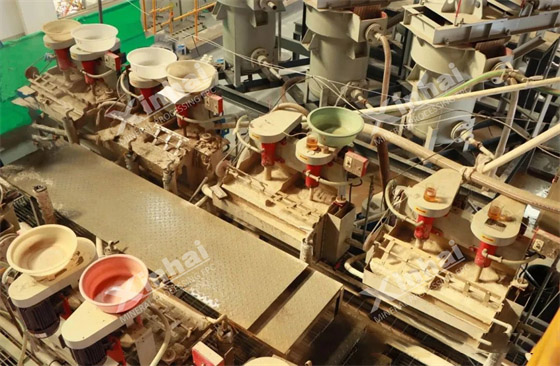
04Test results
The test results show that the flotation process can be used to obtain a phosphorus concentrate with a yield of 62.10%, a P₂O₅ grade of 30.50%, and a recovery of 76.30%, as well as a phosphorus concentrate with a SiO₂ content of 4.03% and an MgO content of 1.56%. The overall index is good, and the process effect is stable.
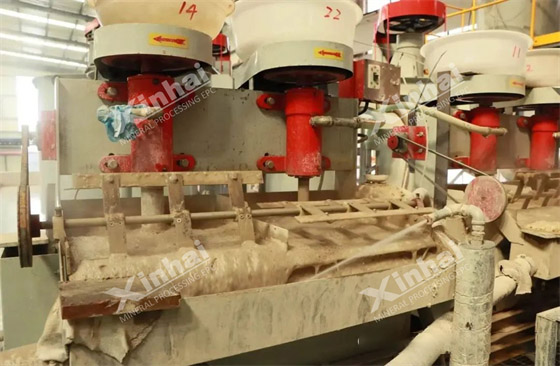
This pilot test of expanding continuous colloidal phosphorite beneficiation has verified the feasibility of the flotation process and its high efficiency in treating complex colloidal phosphorite, with stable process flow and excellent separation indexes. This provides solid technical support for the subsequent industrialized production.
05Xinhai Mining: Representative Mineral Processing Projects
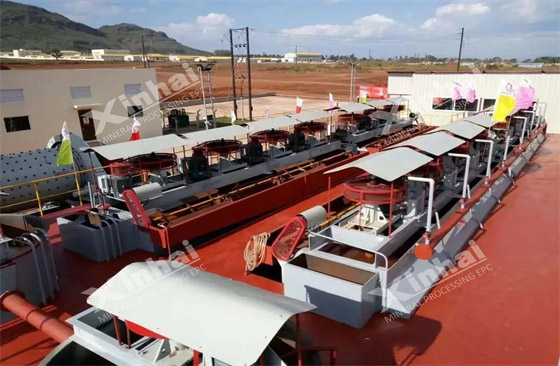
Uganda 720t/d Phosphorus Ore Beneficiation Plant Project
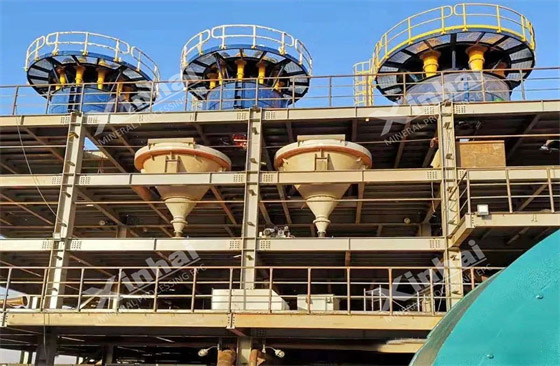
Guinea 15,000t/d Gold Ore Beneficiation Plant Project
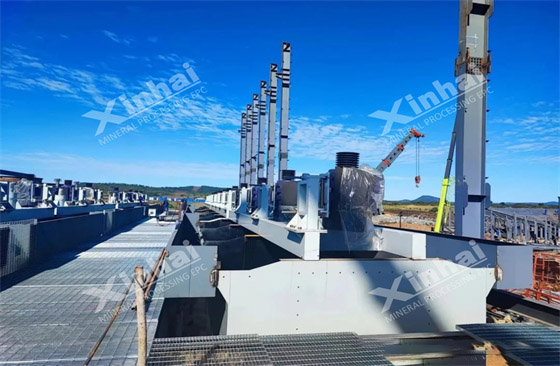
Zimbabwe 2 Million t/a Lithium Ore Beneficiation Plant Project
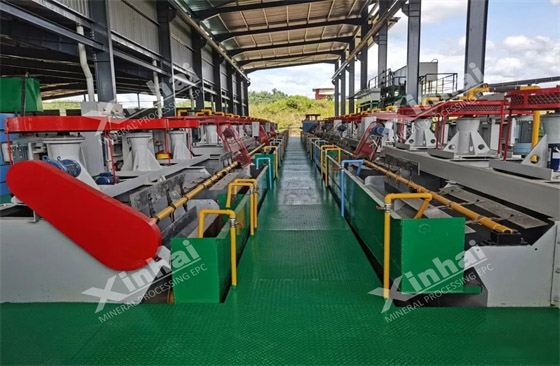
Malaysia 550t/d Lead-Zinc Ore Beneficiation Plant Project
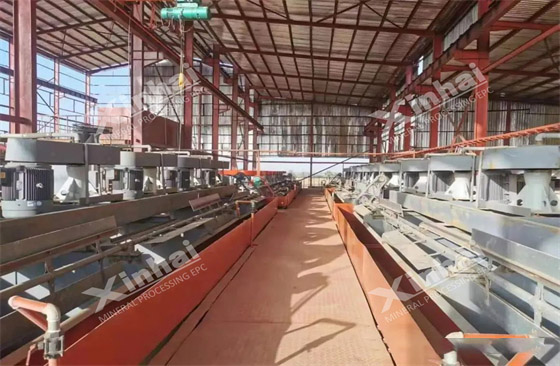
Nigeria 1,000t/d Copper-Silver Ore Beneficiation Plant Project
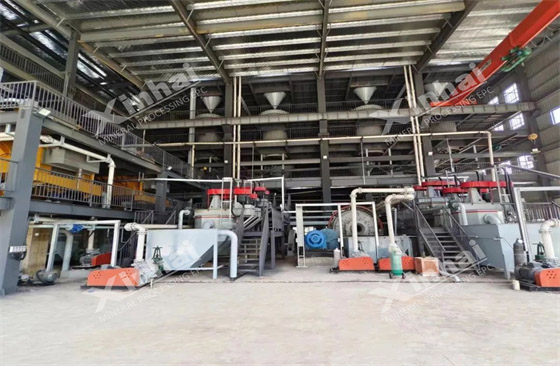
Hubei 0.9 Million t/a Quartz Sand Beneficiation Plant Project