As is known to all, the iron ore is a strategic mineral resource that is widely used at present. However, the iron tailings are also increasing year by year in the iron ore development process, which inevitably brings a series of problems, further stimulates the development in the iron ore development process of iron tailings treatment.
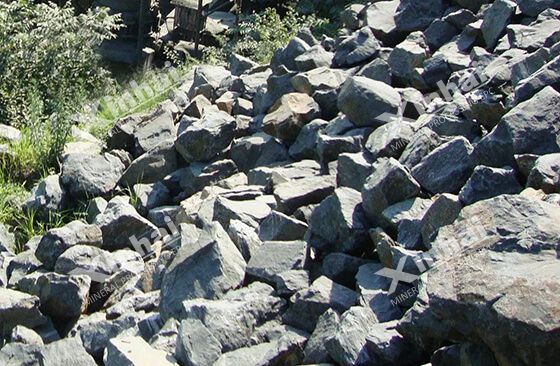
At present, there are three common iron tailings treatment methods: first is the iron tailings reprocessing, that is to recycle the useful minerals in the tailings. Second is the tailings dry stacking, that is to reutilize the tailings after dry discharge. Third is goaf filling with iron tailings.
Use the table of contents below to navigate through the guide:
01Iron tailings treatment - iron tailings reprocessing
According to statistics, the average grade of iron tailings in China is more than 11%, and some mines adopted extensive mining in the past. According to the average grade of total iron, there are 800 million tons of iron in China's iron tailings, which is a very valuable wealth. In the case of increasing shortage of iron ore resources, it is particularly important to strengthen the iron tailings reprocessing to recover iron.
According to the different properties of iron tailings, the magnetic separation and gravity separation methods are often used to recover the minerals from the iron tailings.
magnetic separation method
In some iron tailings, the iron occurs in magnetite, hematite and limonite with weak magnetism, while the gangue minerals are mainly non-magnetic minerals (such as quartz, calcite). Their magnetic difference determines that the magnetic separation method can be used to recover the iron in the tailings.
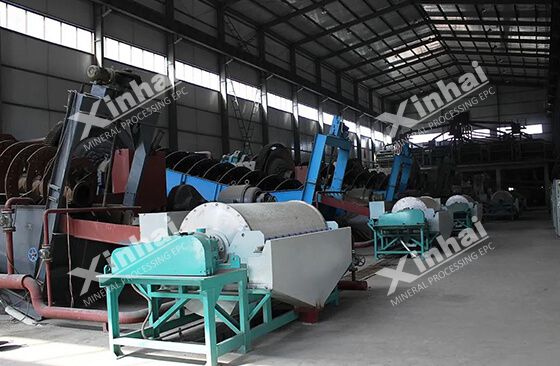
After 2-3 stages of magnetic separation (for example, adopt the high gradient magnetic separation method to pre-enrich the magnetic minerals, and use the shaking table process or centrifuge process), the iron concentrate or ilmenite concentrate can be obtained.
gravity separation method
When recycling the iron from iron tailings by gravity separation, the spiral chute is used for the pre-discharging of iron tailings, and the shaking table is used for the reprocessing of high intensity magnetic concentrate.
When processing the fine ore, the concentrate recovery of the shaking table is low, so the centrifuge can often be used with high intensity magnetic separator at this time, which is suitable for the quality improvement of 35-45 grade iron concentrate.
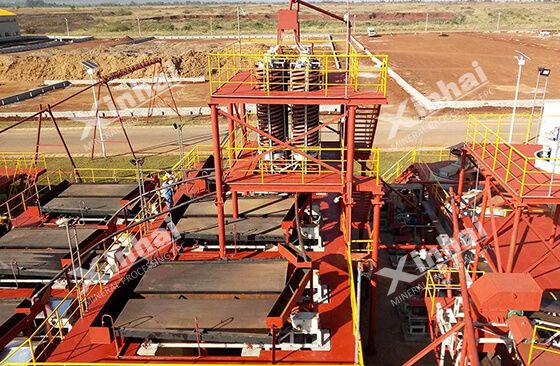
02Iron tailings treatment - iron tailings dry stacking
There are two main iron tailings discharging methods: wet discharging and dry stacking.
The iron tailings wet discharging is a traditional tailings discharging mode with many hidden dangers, which has been gradually eliminated. The tailing dry stacking is a new tailing treatment technology emerging in recent years, which relieves the pressure of tailing reservoir capacity, reduces the safety risks of tailing pond and increases the means of tailing reuse.
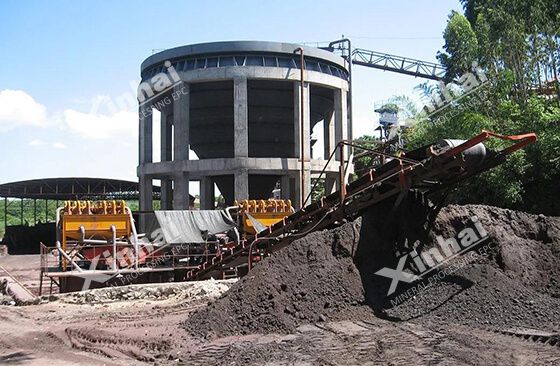
Generally, the tailings dry stacking system is mainly composed of slurry pump, hydrocyclone, efficient improved thickener, high frequency and high efficiency dewatering screen, filter press and slurry conveying device.
The tailings are transported by slurry pump to the hydrocyclone for concentration and classification. The hydrocyclone sand setting enters the high frequency and efficient dewatering screen for dehydration treatment, and the overflow enters the efficient improved for concentration treatment. The coarse tailings treated by dewatering screen are transported to the tailings yard for storage by belt conveyor. Among them, the tailings after concentrated by the efficient improved thickener are transported to the filter press by the slurry pump, and the filter cake is self-unloaded to the belt conveyor, the fine tailings are transported to the tailings yard for storage.
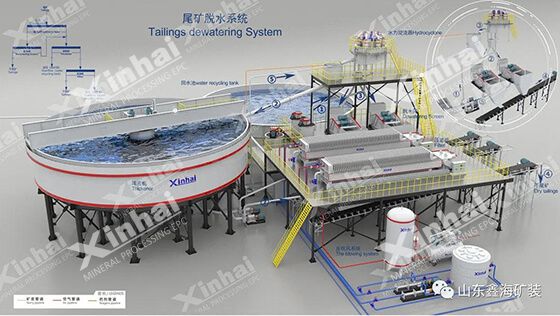
The iron tailings dry stacking method greatly saves the construction cost and routine maintenance cost of traditional tailings pond, realizes the full utilization of backwater, and avoids the risk of tailings pond. In the early stage of construction cost of tailings storage facilities, the tailings dry stacking saves about 30%, and the amount of tailings stored on the same land area increases about 20-30%. In the later comprehensive recovery and utilization of tailings, the dry stack tailings are easier to be recovered and utilized, which is in line with the current national policies for tailings discharging, laying a foundation for the realization of free-tailings and green mine development.
03Iron tailings treatment - goaf filling
In recent years, adopting the iron mine tailings to fill the goaf for ecological restoration has been widely used with the rapid development of backfill mining method. Considering that the terrain of some mines is not suitable for the construction of tailings ponds, it provides an effective and economic method to fill the goaf with iron tailings.
There are two common methods for filling goaf with iron tailings:
whole tailings cement filling technology
The dehydrated iron tailings are mixed with cement and fly ash to form filling aggregate, and the filling slurry is sent to the mining and filling area by the pipeline gravity flow.
high water consolidation filling technology
The material mainly composed of aluminate and sulfur-aluminate and another material mainly composed of anhydrite, quicklime and coagulant are pulped and transported respectively. Before filling, the filling slurry is mixed, and then sent to the goaf by the pipeline.
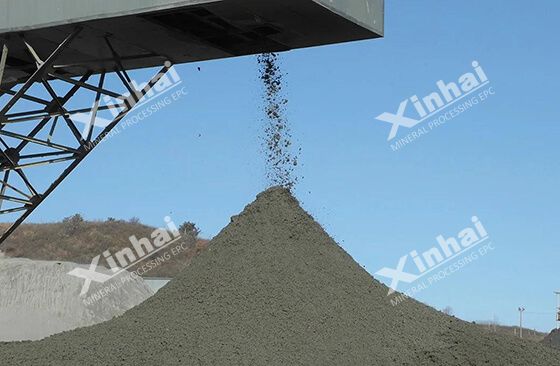
These are the common iron tailings treatment methods. Optimizing the iron tailings treatment and carrying out the comprehensive recovery can make full use of mineral resources and realize the effective unity of resource benefits, economic benefits, social benefits and environmental benefits. In practical application, it is suggested to comprehensively consider the nature of iron tailings, tailings scale, return on investment and other conditions to determine the appropriate treatment and comprehensive utilization of iron tailings.