Malachite is a carbonate mineral, known as basic copper carbonate, which often coexists with other copper minerals. Due to the relatively complex embedded particle size of malachite, the sorting process is more difficult. At present, flotation is the main method for sorting malachite. At the same time, as a kind of copper oxide ore, malachite is essentially a mineral body formed by long-term oxidation of sulfide ore in nature and erosion of groundwater. In this process, a large amount of clay material will be produced and a large amount of slime will be formed, which will have an adverse effect on the flotation process. This article will take you to understand the influence of slime on malachite flotation and the solution.
Use the table of contents below to navigate through the guide:
01The influence of mineral slime on malachite
Ore slime has the physical and chemical characteristics of small mass and large specific surface area, which poses a series of problems for malachite flotation. The particle size of malachite ore slime is generally below 20μm. Fine particles have small mass and low momentum, so the probability of collision with air bubbles is small, the flotation rate is low, and the recovery rate is low. At the same time, it also causes fine particles to mix and reduce the grade of concentrate.
The impact of slime on malachite flotation is mainly manifested in two aspects: competitive adsorption with flotation reagents and mutual coagulation of slime cover.
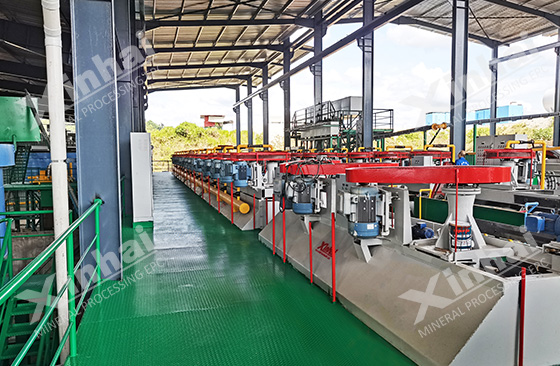
1. Competitive adsorption between slime and flotation reagents
Ore slime has a large specific surface area and high surface energy, which intensifies the non-selective agglomeration between gangue and useful mineral particles. Therefore, the adsorption amount of the agent on the surface of the ore particles increases, which increases the dosage of the agent and reduces the selectivity of the agent.
2. Slime cover and mutual coagulation
The essence of the slime cover is that fine ore particles and coarse ore particles coagulate under the action of static electricity. When the surface potential of the two particles is opposite or the potential is the same but the value is greatly different, it will cause the mud cover phenomenon. The non-selective cover of slime is extremely harmful to the dispersion of ore particles. It reduces the adsorption capacity of reagents on the surface of minerals during flotation, hinders the attachment of air bubbles to useful minerals, and significantly reduces the surface differences of sorted particles. Gangue capping on the useful minerals reduces the concentrate grade, and useful mineral capping on the gangue reduces recovery.
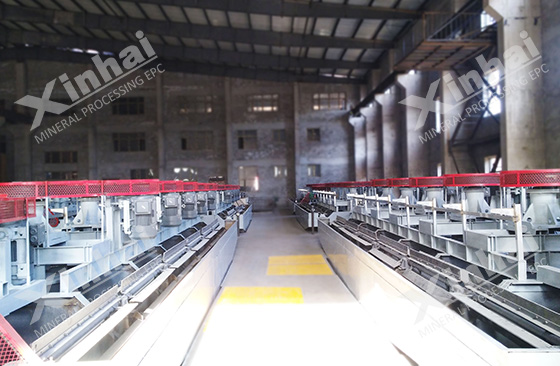
02Improve the malachite flotation effect scheme
Usually, in malachite flotation, in order to reduce the adverse effect of ore slime on malachite flotation, the following four schemes are often used:
1. Desliming pretreatment
There are many methods of desliming in industrial production, such as desliming hopper, spiral classifier, spiral chute, hydrocyclone, cone classifier, shaker, etc., or a combination of some two or several types. Through the desliming process, the environment of the mine rack can be significantly improved and the separation effect can be improved. However, for the ore with very complex distribution, the existing equipment cannot effectively separate the ore slime from the useful minerals.
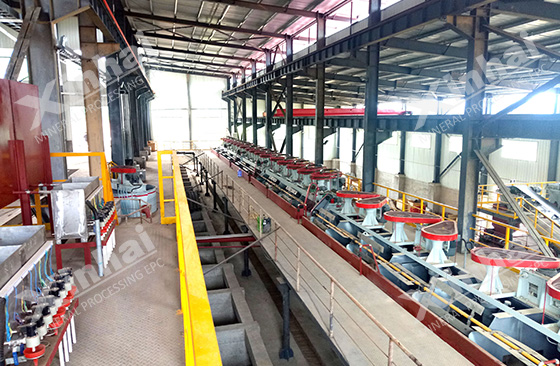
2. Dosing in sections
Dosing in stages is a common method for flotation of malachite ore, which can improve the utilization efficiency of chemicals and keep the concentration of chemicals in the pulp at an ideal level in each stage of flotation. Fundamentally speaking, dosing in stages prevents the mud from absorbing all the medicine at one time. By increasing the number of stages of dosing, the selectivity of the medicine can be amplified, and the adverse effects caused by too fine gangue minerals can be compensated.
3. Low concentration flotation
In malachite flotation, ultra-fine muddy minerals have a large specific surface area. Fine-grained minerals seriously affect the dispersion of the pulp. In essence, the fine mud increases the viscosity of the pulp suspension, increases the friction between particles, and deteriorates the flotation. Flotation with a relatively dilute pulp concentration can improve the fluid characteristics of the pulp, enhance the dispersion of ore particles, reduce the covering of the slime on the useful minerals, and improve the efficiency of the chemical agent.

4. Add dispersant
Common dispersants are sodium hexametaphosphate (SHMP), Na2CO3 and water glass. The dispersant can solve the cover of the slime on the useful minerals, prevent the fine mud from agglomerating, and reduce the viscosity of the pulp. However, the effect of excess sodium hexametaphosphate is not obvious. It will seriously reduce the flotation recovery rate, mainly because sodium hexametaphosphate can significantly reduce the adsorption amount of collector on the mineral surface, so the use of sodium hexametaphosphate should be reduced as much as possible when the mineral dispersion is ideal. quantity.
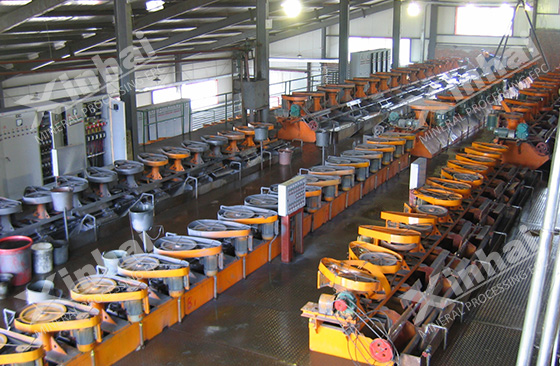
The influence of ore slime on malachite flotation and the solution are introduced above. The properties of malachite in different regions are different, and the particle size is different. The appropriate slime removal method should be selected according to the actual situation. You can also consult manufacturers with professional flotation technology to try to improve the flotation index as much as possible.