When different types of ores are processed and sorted, different beneficiation methods will be chosen, among which flotation is one of the commonly used methods. Flotation is an efficient separation method with a wide range of applications and strong adaptability. It can be used for the separation of various non-ferrous metals, rare metals and non-metallic ores. In order to obtain an efficient flotation process and flotation effect, one should understand how to select the flotation principle process and structure. The following will introduce you to the principle process and structure of ore flotation process to help you better optimize the flotation system.
Use the table of contents below to navigate through the guide:
01How to choose the flotation principle process?
There are two aspects that need to be considered when selecting a flotation process. The first is the number of stages in the flotation process, and the second is the flotation sequence of useful minerals.
Number of flotation process stages
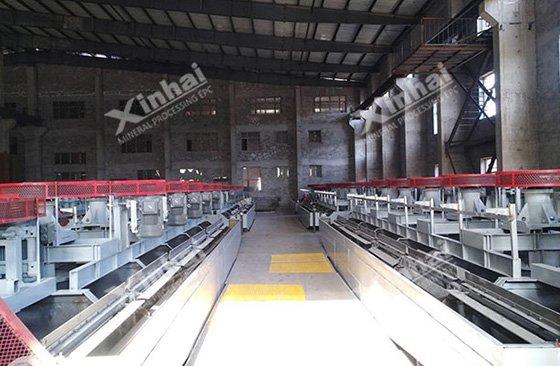
(flotation process)
The number of stages in the flotation process can be one, two or more stages. The number of stages is related to the dissipation particle size characteristics of useful minerals and the muddying situation during the grinding process. In production practice, the flotation process commonly used in mineral processing plants is mainly one-stage flotation and two-stage flotation.
(1) One-stage flotation process: After the ore is ground, it directly enters the flotation stage, and then the concentrate product is obtained. There is no need to re-grind after flotation. This flotation process is mainly suitable for processing ores that are relatively uniformly disseminated with useful minerals. This process can be applied to crystalline apatite ores in which phosphorus-containing minerals are dispersed in coarse or medium grains.
(2) Two-stage flotation process: This is a staged flotation process. This flotation process can effectively reduce the over-crushing and mudification of useful minerals and gangue in the ore. After stage flotation, the gangue can be discharged as tailings with a coarser particle size, which saves a lot of grinding costs and improves the flotation index. The staged flotation process can also preferentially select coarse-grained concentrates with partial monomer dissociation. This process is mainly used to process ores with more complex dissipation of useful minerals. There are two main flotation processes in the grinding stage: one is that the rich tailings in the first stage are reground and then separated, which can be used to treat phosphate ores that are unevenly impregnated with phosphorus-containing minerals; the other is that the first stage of flotation The regrinding and re-selection of medium ore is suitable for processing collophosphate ore where phosphorus-containing minerals are disseminated in fine grains or apatite ores which are partially disseminated in fine grains.
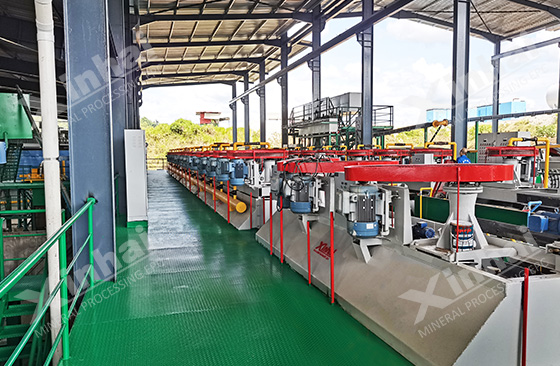
(flotation process)
Flotation sequence of useful minerals
Generally, there are several useful minerals in ores. After determining the principle flotation process, the sequence of various useful minerals must also be solved, which can be divided into two sequences: priority flotation and mixed flotation.
Preferential flotation: When preferential flotation is used, one mineral is floated first, while another mineral is suppressed, and then the other suppressed mineral is activated and flotated.
Mixed flotation: When there are two or more useful minerals in the ore, the mixed concentrate is obtained by flotation first, and then the mixed concentrate is sorted to obtain qualified concentrate. Compared with preferential flotation, mixed flotation can save grinding costs, the use of flotation reagents and the use of flotation cells.
02How to choose the structure of the flotation process?
After determining the flotation principle process of the ore, it is also necessary to consider the internal structure of the flotation process, that is, the number of beneficiation and sweeps during the flotation process and the treatment method of medium ore.
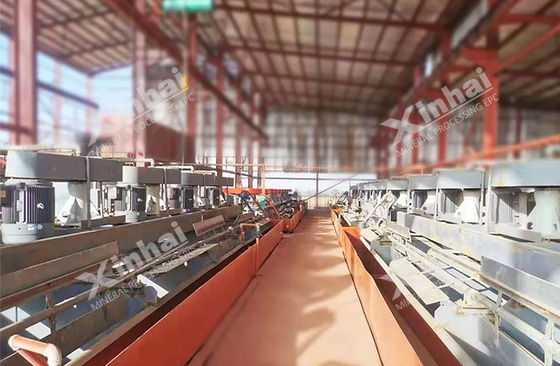
(flotation process)
The number of selections and sweeps is mainly determined by the grade of raw ore, the floatability of useful minerals and the quality requirements of the concentrate. If the grade of raw ore is low, the floatability of useful minerals is good, and the quality of the concentrate is required, the selection time should be extended and the number of selections should be increased. If the raw ore grade is high, the useful minerals have poor floatability and the concentrate quality requirements are not high, the sweeping time should be extended and the number of sweeps should be increased.
The medium ore is mainly the tailings obtained from the beneficiation operation in the flotation process and the foam products obtained by sweeping. The treatment method of medium ore is related to the content of the medium ore conjoint body, as well as the floatability of useful minerals and the quality requirements of the concentrate. Depending on the actual production situation, you can choose to return the middlings to the appropriate location before flotation, return them to the grinding and classification system, or process them separately.
The above is a brief explanation of the flotation principle process and structure. In actual production, the determination and design of the flotation process should be determined based on the characteristics and grade of the ore, production requirements and cost. Xinhai Mining recommends conducting a beneficiation test and analysis of the raw ore before designing the flotation process in order to formulate a suitable separation process, improve production efficiency, and avoid resource waste and equipment purchase costs.