With the global energy structure gradually transitioning to a low-carbon
model, lithium resources—often referred to as "white oil"—play a critical role
in this transformation.
Lithium is especially vital in the development of electric vehicles (EVs),
energy storage systems, and 3C (computer, communication, and consumer
electronics) products, making it a core raw material for the new energy
industry.
Among lithium-bearing minerals, spodumene has become a key source for
producing lithium concentrate due to its high lithium content and large-scale
deposits. However, spodumene must first be processed through mineral
beneficiation before entering the smelting stage.
So, how is spodumene processed into lithium concentrate? This article
provides a detailed explanation of the spodumene beneficiation process.
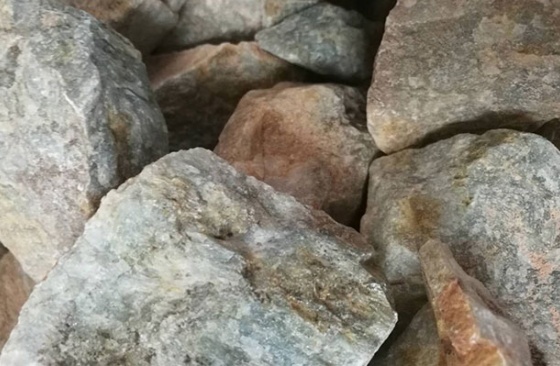
Use the table of contents below to navigate through the guide:
01Spodumene Classification
1. α-Spodumene and β-Spodumene
Spodumene exists in two phases: α-spodumene and β-spodumene.
α-spodumene is monoclinic, dense, stable, and chemically
inert, making it difficult to react with acids or bases. Its direct acid
leaching rate is extremely low. Therefore, the crystal structure must be
destroyed by high-temperature calcination, converting it into the β phase.
β-spodumene is hexagonal in structure, with a loose and
porous lattice and significantly higher reactivity. The leaching rate using the
sulfuric acid method can exceed 90%. Additionally, thermal conversion to
β-spodumene reduces hardness, thereby decreasing grinding energy consumption by
approximately 40%.
2. High-Grade and Low-Grade Spodumene
Spodumene with Li₂O ≥ 1.5% is classified as high-grade, while spodumene with
Li₂O < 1.0% is considered low-grade.
High-grade spodumene has a simple mineral composition, and
its boundary with gangue minerals is well-defined. A small amount of collector
is sufficient to produce a concentrate that meets grade requirements.
The main challenge in processing high-grade spodumene lies in the tendency to
produce fine particles during the fine grinding stage, which can interfere with
flotation performance.
If the ore contains a significant amount of iron-bearing minerals, a magnetic
separation step is necessary, which increases the complexity of the
flowsheet.
Low-grade spodumene is finely disseminated and exhibits
strong similarities with gangue minerals, making it difficult to separate.
Therefore, multiple stages of desliming and concentration are required before
the concentrate grade meets the required standard.
02Spodumene to Lithium Concentrate Processing
1. Ore Pretreatment
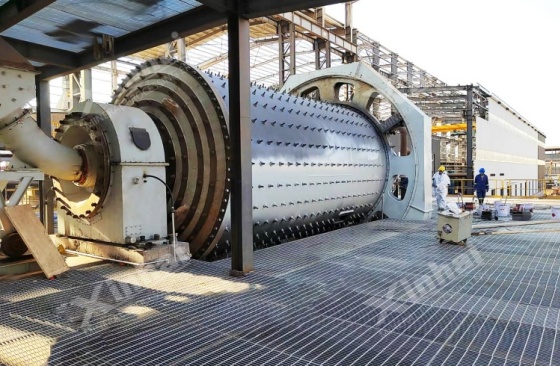
Crushing and Screening: The spodumene ore is first crushed
by a jaw crusher, followed by medium and fine crushing using a cone crusher. The
crushed material is then screened using a vibrating screen. Oversized material
is returned to the cone crusher for re-crushing, while undersized material
proceeds to the grinding and classification stage.
Grinding and Classification: The screened spodumene is fed
into a ball mill for grinding and subsequently classified by a hydrocyclone. The
fine slurry flows directly to the flotation stage, while the coarse particles
are returned to the ball mill for further grinding.
2. Beneficiation Process
Flotation (Mainstream Process): Flotation is the primary
method used to separate spodumene from gangue minerals. Prior to flotation,
desliming is conducted to remove fine mud. Then, pH regulators and collectors
are added. In the flotation cell, spodumene attaches to air bubbles and rises to
the surface under agitation and aeration. The resulting froth is collected as
lithium concentrate.
Reagent System: Common pH regulators include sodium
hydroxide and sodium carbonate. Collectors typically include oleic acid (a fatty
acid) or cationic oxidized paraffin soap. Gangue minerals are suppressed using
depressants such as starch or dextrin.
Flotation Flow: The flotation circuit typically includes
roughing → scavenging → cleaning, with multi-stage flotation employed to
maximize recovery.
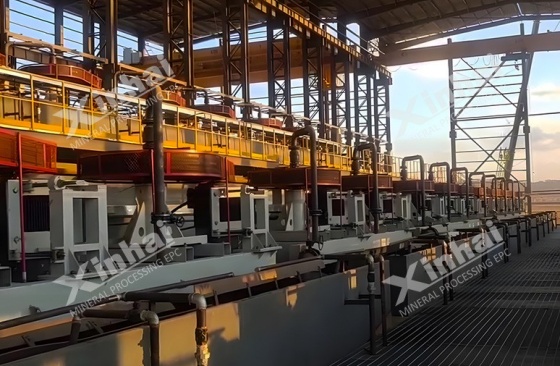
Gravity and Magnetic Separation (Auxiliary Processes): If
the ore contains a significant amount of fine-grained iron minerals, magnetic
separation is applied before flotation to remove iron impurities and prevent
interference in downstream flotation. If the gangue minerals contain heavy
impurities such as barite, a gravity separation stage may be introduced ahead of
flotation to remove these heavy components.
3. Concentration and Dewatering
The flotation concentrate undergoes further thickening, dewatering, and
drying. First, the lithium slurry is sent to a high-efficiency deep cone
thickener, which increases the slurry concentration through flocculation and
sedimentation.
The thickened slurry is then dewatered using a plate-and-frame filter press
or a vacuum filter, reducing the moisture content to below 20%. Finally, the
product is dried in a rotary kiln or similar drying equipment to produce
finished lithium concentrate.
03Challenges in Spodumene Processing Technology
1. Flotation Reagents
Flotation is the core process in spodumene beneficiation. The performance of
flotation reagents directly impacts the grade and recovery rate of lithium
concentrate. However, current reagents face challenges such as poor adaptability
to low-temperature environments and difficulty in effectively depressing gangue
minerals. The application of composite low-temperature collectors, combined with
nanoemulsion technology, can enhance reagent adsorption on mineral surfaces
under low-temperature conditions, improving flotation efficiency.
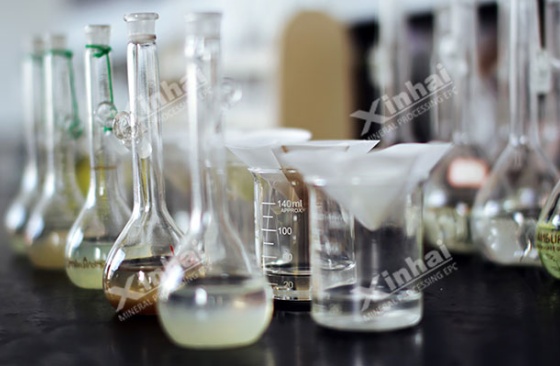
2. β-Spodumene Activation Technology
Natural α-spodumene is highly inert and must be activated—typically through
phase transformation—into β-spodumene to facilitate lithium extraction.
Traditional high-temperature roasting methods have high energy consumption and
operating costs. Emerging technologies such as microwave roasting and
mechanochemical activation offer more energy-efficient alternatives to
conventional roasting, reducing operational costs while improving conversion
efficiency.
3. Comprehensive Utilization of Tailings
Spodumene ores are often associated with gangue minerals such as feldspar and
quartz. The efficient utilization of tailings and comprehensive recovery of
valuable by-products have become key industry concerns. For instance, a
spodumene tailings project in Xinjiang adopts a combined magnetic
separation–flotation process to recover feldspar and quartz, resulting in an
annual output value increase of over 120 million yuan.
The above outlines the processing flow for converting spodumene into lithium
concentrate, as well as recent technical advancements in overcoming processing
challenges. Today, intelligent concentrator plants use AI-based dynamic
optimization systems to improve lithium recovery rates, reduce reagent
consumption, and enhance overall resource utilization.
Conclusion
Xinhai Mining offers full-process spodumene beneficiation EPC+M+O services,
helping clients to build intelligent, efficient, and sustainable concentrator
plants. If you are interested, please feel free to contact us.