Magnetic separation is one of the main beneficiation methods of iron ore extraction. And magnetic separator is the main equipment of this method. In actual production, the operation of the magnetic separator has a very obvious impact on the separation effect of iron ore.
The main operating factors include the thickness of the magnetic separator feed layer, the magnetic separator cylinder speed, the ore feeding speed and the water inflow. This article will analyze the above 4 key points of operation to teach you how to increase efficiency of iron ore magnetic separation process.
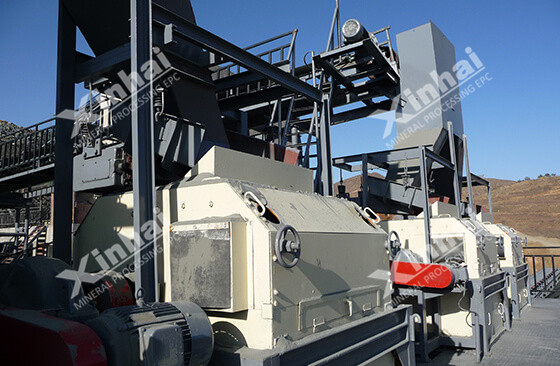
Use the table of contents below to navigate through the guide:
01Adjust Feed Layer Thickness
Feed layer thickness is the feeding capacity, which is closely related to the particle size and magnetic mineral content of the raw ore fed into the magnetic separator. Generally, the feed layer of coarse-grained iron ore is thicker than that of fine-grained iron ore. The thickness of the feed layer for coarse-grained iron ore should be about 1.5 times the upper limit of particle size, while for medium or fine-grained iron ore, the thickness of the feed layer can reach 4 to 6 times the upper limit of particle size.
In the case that the content of magnetic minerals in the original iron ore is small, the thickness of the feeding layer should be appropriately reduced to avoid the magnetic ore particles located in the lower layer from being unable to be affected by the magnetic force and reduce the impact on the recovery rate of magnetic minerals. Similarly, when the content of magnetic minerals is relatively large, the thickness of the feeding layer can also be appropriately increased.
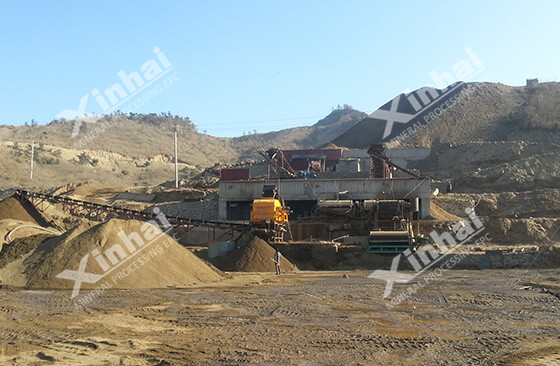
02Choose Proper Magnetic Separator Cylinder Speed
The magnetic field strength of the iron ore magnetic separator barrel forms a regular distribution according to the design requirements. Taking the permanent magnet separator as an example, the magnetic field strength will not change the magnetic field gradient due to the change of the current. Under this condition, controlling the rotating speed of the magnetic separator cylinder is one of the important operations to adjust the separation index, and its speed is mainly determined by the iron ore raw material particle size and operating requirements.
The rotating speed of the cylinder of the magnetic separator is mainly controlled by the frequency converter. When the feeding iron ore raw minerals have strong magnetic properties, the frequency conversion speed should be reduced. On the contrary, when the feeding iron ore raw minerals have weak magnetic properties, the frequency conversion speed will be should be accelerated. In addition, under the condition of wet magnetic separation, the frequency conversion speed is lower than that of dry magnetic separation, and the rotating speed of the cylinder is also faster than that of dry magnetic separation. During the iron ore fine-grained scavenging, the frequency conversion speed is lower than that of the iron ore concentration, and the rotating speed of the cylinder is also faster.
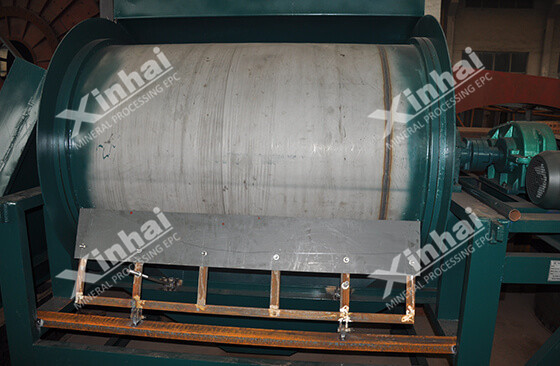
03Adjust Magnetic Separator Feeding Speed
The feeding speed of the magnetic separator has a direct impact on the residence time of iron ore particles in the magnetic field and the mechanical force. At the same feeding speed, weak magnetic iron minerals are weaker than strong magnetic iron minerals in the magnetic field, resulting in a decrease in recovery rate. Therefore, when separating iron ores with weak magnetic properties, the feeding speed should be appropriately reduced.
In different iron ore beneficiation stages, the feeding speed of the magnetic separator is different. During the concentration stage, the raw iron ore has many single minerals and strong magnetic properties, so the ore feeding speed can be appropriately increased. However, in the scavenging stage, the iron ore raw materials have more conjoined minerals and weaker magnetic properties. At this time, the ore feeding speed can be reduced to improve the recovery rate.
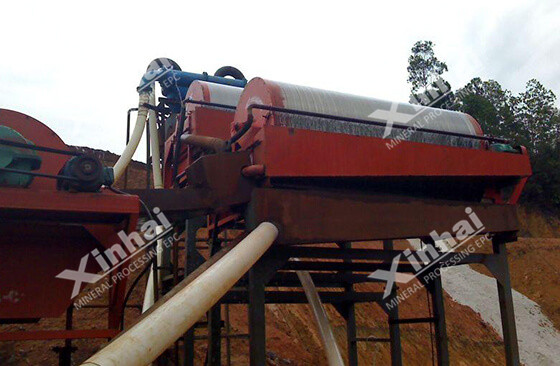
04Control Magnetic Separator Water Inlet
When wet magnetic separation is used, the water inlet control of the magnetic separator is very critical to the stability of the separation effect. It requires a reasonable opening of the water inlet pipe of the magnetic separator to avoid excessive water inlet pressure. At the same time, the control of water concentration is also very important. Excessive circulating water concentration will affect the dispersion and sedimentation effect of iron ore, thereby affecting the concentrate grade. It is ideal for the circulating water concentration to be below 10%. If the circulating water is turbid, precipitation is required for reuse.
To Wrap Up
The above are the four important operating points of the magnetic separator for iron ore magnetic separation. It is suggested that the beneficiation test should be done well before formulating the iron ore beneficiation solution. In daily operation, regular observation and timely adjustment should be made according to the situation to ensure stable iron ore beneficiation effect and economic benefit.
If you have any question about the above, or want to customize your iron ore processing solution, please leave your message or contact the online service.