Soda feldspar is a key raw material widely used in glass manufacturing,
ceramics, and the chemical industry. However, raw soda feldspar ore often
contains impurities such as quartz, mica, and iron-bearing minerals. To
effectively increase the Al₂O₃ content and reduce impurity levels, ore washing
is a crucial step in the beneficiation process.
When designing a soda feldspar washing plant, Xinhai Mining fully considers
the equipment compatibility and process integration. The resulting process flow
is highly efficient, energy-saving, and features a high degree of
automation.
Use the table of contents below to navigate through the guide:
01Key Equipment for Soda Feldspar Washing Plant
In the processing of soda feldspar, there are three main challenges in the
beneficiation process:
The physical properties of soda feldspar and potassium feldspar are similar,
making separation difficult;
It is challenging to remove fine-grained clay minerals;
Efficient removal of impurities such as iron and titanium remains
complex.
To overcome these challenges, the key equipment in a soda feldspar washing
plant includes:
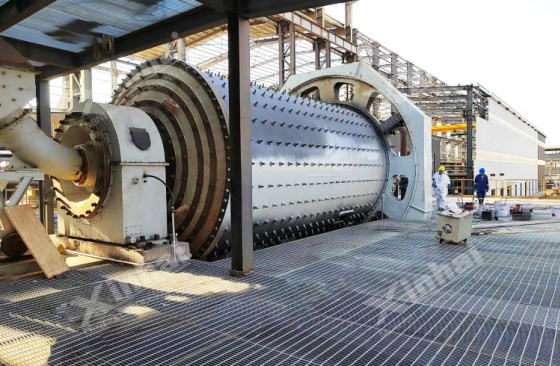
1. Crushing and Grinding Equipment
Jaw Crusher: Used for the primary crushing of soda feldspar
ore, reducing the particle size to below 100 mm. Hydraulic jaw crushers are
recommended for their large reduction ratio and low energy consumption.
Cone Crusher: Responsible for secondary and tertiary
crushing, further reducing the ore to below 30 mm. The laminated crushing
principle ensures a more uniform product size, which is suitable for medium-hard
ores like soda feldspar.
Ball Mill: The crushed ore is sent to a ball mill for wet
grinding to a fineness of -200 mesh. Since iron impurities can significantly
affect concentrate quality, it is advisable to use rubber linings in the ball
mill to minimize iron contamination.
Classification Equipment: Ball mills are often paired with
hydrocyclones or spiral classifiers to form a closed-circuit grinding and
classification system.
2. Beneficiation (Sorting) Equipment
Trough Scrubber:
Used to remove surface-attached clay, fine mud, and other impurities,
especially effective for weathered feldspar ore. Through impeller stirring, it
peels off surface clay, achieving over 85% desliming efficiency on high-mud
ores.
Magnetic Separation Equipment:
Permanent Magnetic Drum Separator: First-stage separation, with a magnetic
field strength of 0.1–0.3 T, for removing strongly magnetic minerals.
Wet High-Gradient Magnetic Separator (HGMS): Second-stage fine separation,
with 1.0–1.5 T field strength, to remove weakly magnetic minerals such as
hematite and ilmenite.
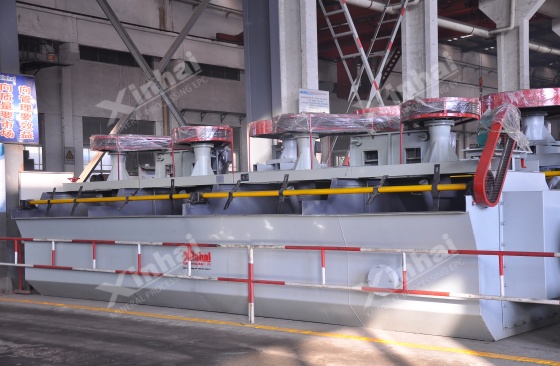
Flotation Equipment:
Used to remove gangue minerals such as quartz and mica.
For quartz separation: Adjust pH to acidic, use hydrofluoric acid as an
activator and amine collectors to float feldspar while inhibiting quartz.
For mica separation: Adjust pH to alkaline and use cationic collectors to
float mica.
Equipment recommendation: Use KYF flotation cells for roughing and scavenging, and flotation columns for cleaning to
improve concentrate grade.
Photoelectric Sorter:
Applied to separate potassium feldspar from soda feldspar based on
differences in color and reflectivity. Using high-speed air valves, it achieves
sorting accuracy over 90%.
3. Dewatering and Drying Equipment
Thickener and Filter Press: After sorting, the concentrate pulp is thickened
to about 50% solid content using a thickener and then dehydrated by a filter
press to reduce the moisture content to ≤15%.
Rotary Dryer: Finally, a rotary drying kiln reduces moisture to below 5%,
ensuring ease of transportation and storage.
02Soda feldspar Washing Plant Process Flow
According to the ore type and impurity composition, soda feldspar can be
divided into two main types:
(1) coarse-grained weathered ore and
(2) fine-grained disseminated ore.
Below is a typical process flow for treating each type.
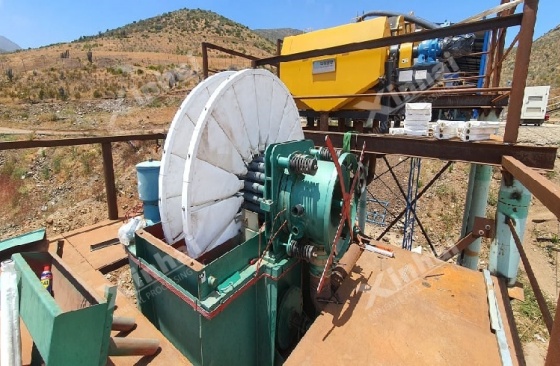
1. Coarse-Grained Weathered Ore
Process Flow:
Soda feldspar ore → Jaw crusher (crushed to ≤50 mm) → Drum ore washing screen
(with water flushing and screening) → Trough scrubber (clay removal) → Spiral
classifier (desliming) → Dry magnetic separator (for removal of strongly
magnetic iron minerals) → Concentrate dewatering → Final product
This process relies primarily on physical cleaning methods, features low
equipment investment, and is suitable for the preliminary treatment of low-grade
ores.
The typical concentrate quality can reach:Al₂O₃: 20–22%;Fe₂O₃: 0.5–0.8%.
2. Fine-Grained Disseminated Ore
Process Flow:
Albite ore → Jaw crusher → Cone crusher → High-pressure grinding roller
(HPGR) (to ≤3 mm) → Ball mill (80% passing -200 mesh) → Hydrocyclone
classification → Desliming (removal of fine particles <10 μm) → High-gradient
magnetic separation (removal of iron and titanium impurities) → Flotation (HF
activation of albite; reverse flotation of quartz) → Thickening → Filter press →
Drying → Final concentrate
This process integrates magnetic separation and flotation, requiring precise
control of pH levels and reagent dosage.
The final concentrate meets high-end ceramic raw material standards, with
specifications of:Al₂O₃ ≥ 26%;Fe₂O₃ ≤ 0.3%.
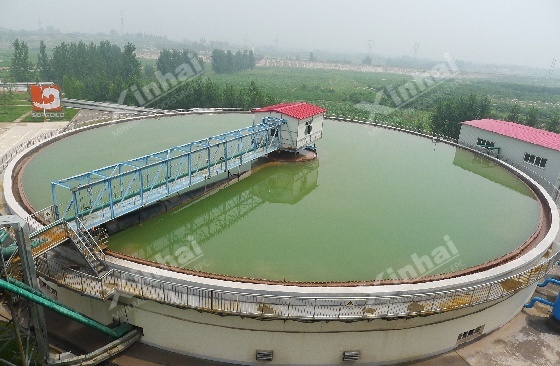
03Soda feldspar Washing Plant Project Case
The soda feldspar washing plant project undertaken by Xinhai Mining is
located in Hebei Province, China. The main valuable minerals are soda feldspar
and potassium feldspar, with a combined content of 60–80%.
The major gangue minerals include:Quartz (10–30%);Biotite (1–5%);Muscovite
(1–5%). With trace amounts of magnetite and tourmaline.
Crushing and Grinding Stage
The crushing circuit adopts a two-stage closed-circuit process, consisting of
a jaw crusher and circular vibrating screen for primary crushing, followed by a
cone crusher for secondary and fine crushing.
The grinding and classification stage adopts a two-stage closed-circuit
grinding process:
A grate-type ball mill and spiral classifier are used for coarse grinding
An overflow-type ball mill is used for fine grinding
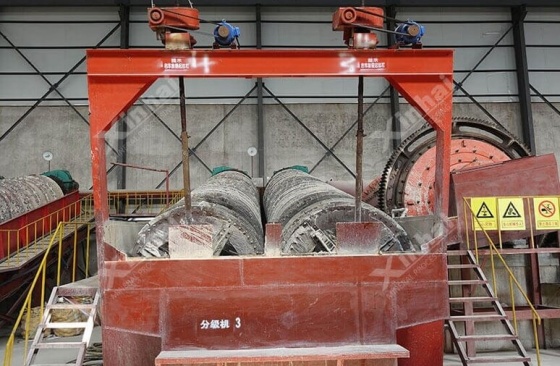
Separation Process
The separation operation involves three key steps:
Medium-intensity magnetic separation
Desliming
Reverse flotation
A magnetic separator is first used to remove magnetite impurities.
The magnetic tailings are sent to a desliming tank to eliminate fine clay
particles.
After desliming, the slurry is sent to a mixing tank, where it is thoroughly
mixed with reagents, and then pumped to the XCF/KYF flotation unit for reverse
flotation, effectively removing iron oxides and mica.
The concentrate is then dewatered using a hydrocyclone and dewatering
screen.
Project Results
Feldspar concentrate yield: 73.37%;Annual output: 87,972 tons of high-quality
feldspar concentrate
Conclusion
This project highlights the key equipment and typical process flow involved
in a soda feldspar washing plant.
With over 30 years of experience in the mineral processing industry, Xinhai
Mining has undertaken thousands of feldspar beneficiation projects, accumulating
a wealth of practical knowledge.
The mineral processing plants designed and constructed by Xinhai feature:High
automation and intelligence levels;Advanced manufacturing technology;Concentrate
grades of Al₂O₃ ≥ 26%, Fe₂O₃ ≤ 0.3%;Recovery rates exceeding 85%, meeting or
exceeding industry-leading standards.
If you are looking for an efficient and reliable solution for soda feldspar
beneficiation, feel free to contact us for customized support.