Most of the naturally occurring ores are in a continuous state and are difficult to utilize directly. A series of technical means such as mineral processing engineering are required to enrich the concentrate. Before using mineral processing operations to enrich concentrates, the grinding operation mainly involves monomer dissociation of useful minerals and gangue minerals to achieve appropriate separation particle sizes. Grinding is the last process before material preparation and separation, and the final product of grinding directly affects the quality of the concentrate. Therefore, increasing the degree of mineral dissociation, reducing the proportion of over-crushed particles, and further improving the uniformity of the particle size of the grinding product can further improve the separation index. Understanding the factors affecting the working process of grinding equipment has an important impact on improving its working efficiency. The following will introduce you to several factors that affect the grinding efficiency of ball mill.
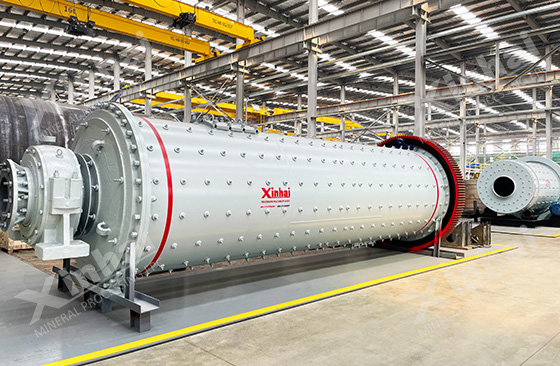
(Ball Mill)
Use the table of contents below to navigate through the guide:
01Grinding concentration on ball mill grinding
Grinding concentration is one of the important factors affecting the working efficiency of ball mill. The influence of grinding concentration is mainly reflected in three aspects: the specific gravity of the slurry, the degree of adhesion of the ore particles around the steel ball and the fluidity of the slurry. The lower the grinding concentration, the faster the fluidity of the slurry, the adhesion of the mineral materials around the steel ball will also be reduced, and the impact and grinding effect of the steel ball on the mineral itself will naturally be weakened. Therefore, the qualified particle size in grinding products does not meet the production requirements. If the grinding concentration increases, the effect will be opposite, which will cause over-grinding problems, causing the minerals to be over-crushed and making it difficult to recover useful minerals.
02Grinding media size on ball mill grinding
Proper media size affects the quality of the grinding product. During the coarse grinding process, the grinding medium makes a throwing motion, which impacts the material. Therefore, it is necessary to select a larger size medium during coarse grinding. During fine grinding, the contact area between the material and the grinding medium needs to be as large as possible to grind the material, so the size of the medium selected for fine grinding is smaller.
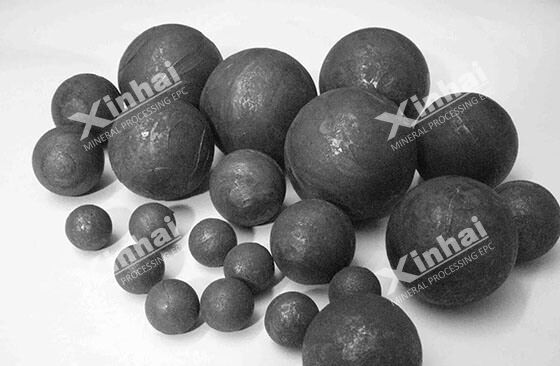
(Grinding media)
03Media filling rate on ball mill grinding
The filling rate of grinding equipment refers to the ratio of the volume of media added to the equipment to the internal volume of the ball mill. The movement state of the medium in the mill is related to the filling rate of the medium. The movement modes of the medium in the ball mill can be divided into three categories: throwing movement, cascading movement and centrifugal movement.
The throwing movement mainly uses the impact force generated by the medium to crush coarse-grained materials.
The cascading movement means that when the ball mill rotates, the medium rolls down as the cylinder reaches a certain height, and the materials are crushed with a grinding force between the medium and the medium and between the medium and the lining plate.
The centrifugal movement means that there is no relative movement between the medium and the lining plate, and it does not have any grinding effect on the material.
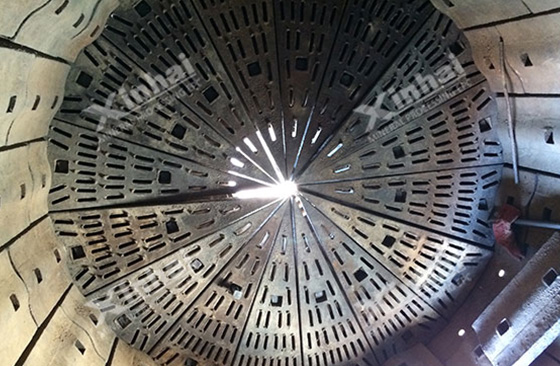
(Ball mill lining plate)
When the media filling rate and friction force are large enough, the grinding media can reach the throwing point along with the lining plate. Generally speaking, as the media filling rate increases, the amount of materials and media in the grinding equipment will also increase, and the equipment production capacity will also increase. However, the filling rate inside the ball mill cannot be too high. An increase in the filling rate will lead to an increase in the number of substances in the inner layer of the cylinder, while the inner grinding balls carry less energy, which is not conducive to the crushing of materials. At the same time, too high a filling rate will increase dielectric loss and reduce equipment production efficiency. Therefore, in actual production, choosing the appropriate equipment media filling rate can greatly reduce the loss of grinding media and power consumption.
04Media materials on ball mill grinding
Grinding media is the most consumed part in the entire grinding process, so it is of great economic significance to increase the wear resistance of the grinding media and reduce the consumption of the grinding media. Grinding media materials can be divided into two categories: one uses metal as the media material, such as cast iron media and steel media. The other type uses hard stones, which are difficult to grind, as the media material. When using a semi-autogenous grinding machine, using hard stones as the grinding medium can reduce grinding costs.
In order to achieve good grinding effect and reduce the consumption of grinding media, the grinding media needs to be hard and have good wear resistance, and it also needs to have enough toughness to ensure that it is not broken when it is impacted in the mill. The metal medium has a high ability to transmit energy. When the metal medium is relatively large, you can get high crushing efficiency and less energy consumption.
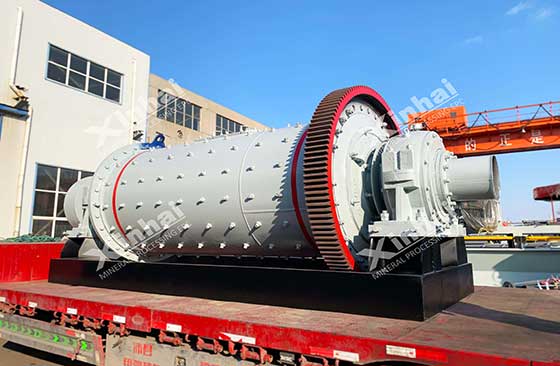
(Ball Mill)
The above are the four factors that affect the grinding efficiency of the ball mill. There may be other factors in actual production, so appropriate adjustments should be made based on actual production conditions. There are many types of ball mills on the market. In order to obtain good grinding effects, it is necessary to select the appropriate ball mill type according to the characteristics of the ore. Xinhai Mining recommends selecting a ball mill based on the ore beneficiation test results, which can reduce equipment costs and achieve higher equipment efficiency.