In the daily production process of the ball mill, due to its complex working conditions, the project takes a long time and is subjected to unstable loads for a long time. At the same time, there will be vibration, shock and additional dynamic load in the process. Over time, it will cause wear or even breakage of the various parts of the ball mill, seriously affecting the normal production of the ball mill. Below we will introduce the reasons for the fracture and the improvement measures from the aspects of the fracture of the connecting bolt of the ball mill hollow shaft, the fracture of the gear shaft of the ball mill, the fracture of the liner of the ball mill and the fracture of the liner bolt of the ball mill.
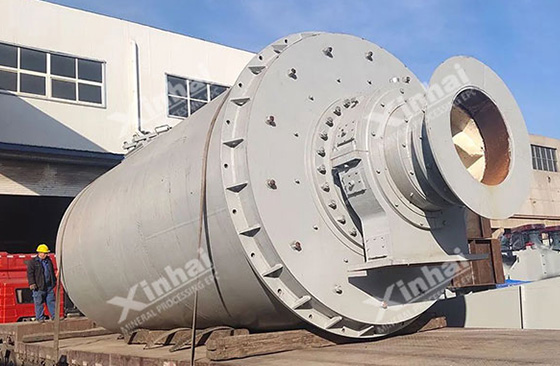
Use the table of contents below to navigate through the guide:
01The connecting bolt of the hollow shaft is broken
During the production process of the ball mill, the connecting bolts of the hollow shaft are loose, and the bolts are not locked in time, or after replacing the new bolts, the slag remaining on the joint surface of the hollow shaft end cover and the mill cylinder is not cleaned in time, all of which cause the hollow shaft of the ball mill to connect. Causes of bolt breakage. In addition, when the ball mill was shut down for maintenance, it was seen that the miller did not use the jack to tighten the cylinder in time, resulting in slight deformation of the cylinder. Or in order to increase the output per hour, adding overloaded grinding bodies to the ball mill to make it run overloaded will also cause the hollow shaft connecting bolts to break.
Improvements:
During the operation and production of the ball mill, it should be operated in strict accordance with the operating procedures. Daily inspection and regular maintenance should be done carefully. After replacing the bolts, the sundries should be cleaned up in time. After repairing, run at full load for 48 hours and stop. Use a jack to tighten the cylinder first, and then check whether the connecting bolts are loose. If it is loose, it should be locked in time. During the operation, it is necessary to strictly control the total load of the grinding body of the mill not to exceed its rated load.
Note that when the ball mill is reinstalled, the hollow shaft can be separated from the cylinder first. Check whether the joint surface of the hollow shaft end cover and the cylinder end cover is smooth. If it is found that there are protrusions on both ends of the bolt hole, it can be smoothed by installing a polishing sheet on an angle grinder. Install after the joint surface is cleaned. During installation, it should be noted that the locking force of each bolt should be consistent to ensure that each bolt is evenly stressed.
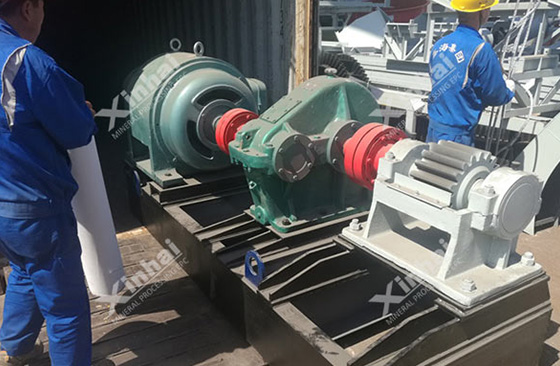
02The gear shaft of the ball mill is broken
The fracture of the gear shaft of the ball mill is mostly caused by long-term operation and fatigue. During daily work, since the gear bearing of the ball mill bears a large bending moment and torque, the bending moment produces normal stress on the shaft, and the torque produces shear stress. These stresses are constantly changing during the operation of the shaft and belong to symmetrical cyclic alternating stresses, and there are additional dynamic loads at the same time. Once encountering vibration, overload, sudden start and brake and multiple heavy load impacts, the shaft is prone to cracks and breaks.
Improvements:
The operating specifications should be strictly enforced, equipment maintenance and maintenance should be strengthened, and regular inspections should be carried out. It is strictly forbidden to overload the ball mill and cause strong impact and vibration.
03The liner of the ball mill is broken
When the ball mill is running, the liner breaks, which is probably caused by the unreasonable ball filling rate and proportion. When the charging rate of steel balls is low, the steel balls will wear more on the liner. Or the proportion of larger steel balls in the steel balls is higher, which will cause a greater impact on the liner, and sometimes cause the liner of the ball mill to break.
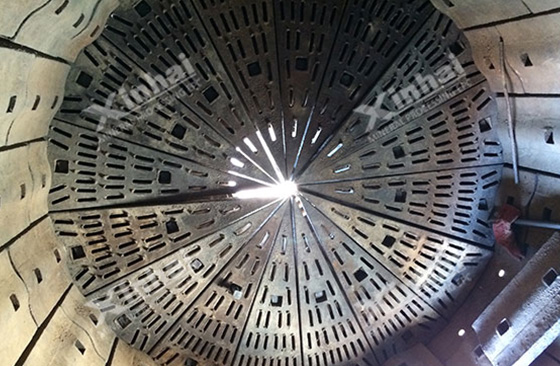
Improvements:
During the production of the ball mill, the balls should be fed strictly according to the requirements, and the size of the balls should be strictly controlled. The filling rate of the ball mill can be determined by referring to the thickness of the liner and the diameter of the steel ball. The suitable filling rate of small and medium-sized ball mills is generally between 35 and 45%. The filling rate of large ball mills is generally between 30 and 35%. In terms of medium ratio, you can refer to the theoretical formula of ball diameter and half to calculate the appropriate ratio of steel balls under different ore hardness and feed particle size.
04The liner bolts of the ball mill are broken
The breakage of the liner bolts of the ball mill is mostly due to the long-term operation of the ball mill, the long-term impact and extrusion of the materials in the cylinder and the steel balls on the liner, resulting in radial and centripetal bow deformation of the liner, which increases the axial tension of the bolts. stress. In addition, when the cylinder of the ball mill rotates, the liner and the cylinder will be displaced relative to each other in a tangential direction, so that the bolts will bear the shear force on the two tangent sections of the cylinder. Under the action of this alternating load, the bolts gradually fatigue, causing cracks, and eventually lead to fracture.
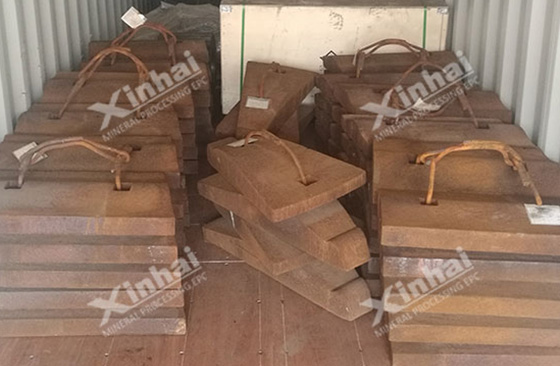
Improvements:
The breakage of ball mill liner bolts is mostly caused by fatigue. Therefore, the anti-fatigue ability of the bolt can be enhanced by increasing the dangerous fracture diameter of the bolt. The bolts are increased by 10mm and multiple washers are added under the bolts (according to the bolt hole size of the liner). Or add some high-pressure rubber asbestos pads on the body surface to enhance its cushioning and reduce the impact force of the liner, thereby reducing the breakage of the liner bolts.
In addition, when installing liner bolts, the pre-tightening force of the bolts should be controlled, neither too large nor too small (generally, the bolts are tightened with a fastening force of 540~2000N·m). Just after it is put into production and operation, it needs to be tightened again every 8 to 12 hours, and the tightening must be repeated many times.
The above are the reasons and improvement measures for the fracture of several ball mill parts. The proportion of investment and energy consumption of ball mills in concentrators are relatively large. Once the accessories break, it will seriously affect the normal operation of the ball mill, and even cause personal injury. In order to reduce the breakage of various parts of the ball mill, the on-site staff must strictly follow the requirements for assembly, and strengthen daily inspection and maintenance. In addition, when purchasing, choose a professional and qualified ball mill manufacturer to prolong the service life of the equipment and avoid economic losses.