Lithium resources are mainly categorized into salt lake brine and hard rock
types. This article focuses on hard rock lithium mining and processing
equipment, as well as the model selection strategies for key machinery. The
mining and processing of lithium ore typically involve five stages: exploration
→ mining → beneficiation → refining (into lithium carbonate/lithium hydroxide) →
battery manufacturing. Among these, investment in mining and processing
equipment accounts for approximately 40% to 60% of the total project cost.
Therefore, understanding the composition of this equipment and the strategies
for selecting appropriate models is particularly important.
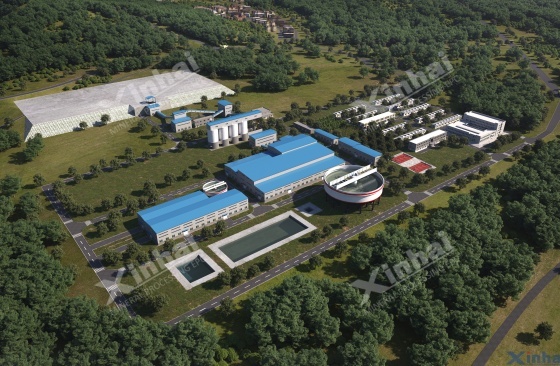
Use the table of contents below to navigate through the guide:
01Lithium Mining Equipment
1. Exploration Equipment
Ground-Penetrating Radar (GPR): Used in lithium ore exploration to detect the
geometry and grade distribution of underground ore bodies. GPR and
electromagnetic instruments are commonly employed. GPR has a detection depth of
50–100 meters with a resolution of ±0.1 meters. Electromagnetic instruments are
suitable for delineating lithium ore targets in complex terrains.
Diamond Core Drill: Utilized for obtaining core samples to analyze lithium
grade (Li₂O content), with a drilling depth of 1,000–2,000 meters.
Portable XRF Analyzer: Enables rapid, on-site determination of elemental
content such as lithium and beryllium, with a detection accuracy of ±0.05%
Li₂O.
2. Open-Pit Mining Equipment
Drilling and Blasting Equipment: Intelligent drilling rigs with a borehole
diameter of 165 mm and automatic positioning accuracy of less than 10 cm are
recommended. Digital electronic detonators can be used for controlled
blasting.
Loading and Hauling Equipment: Hydraulic shovels or electric rope shovels are
suitable for loading; ultra-large mining trucks are recommended for
transportation.
Primary Crushing Station: Mobile jaw crushers are used to crush mined lithium
ore on site, with a typical output particle size of 150 mm.
3. Underground Mining Equipment
Shaft Excavation Equipment: Deep well drilling rigs can achieve a maximum
bore diameter of 8 meters and a depth of up to 1,500 meters.
Ore Mining Equipment: Load-Haul-Dump (LHD) machines are suitable for tunnel
gradients of up to 15°. Raise boring machines can be used for reverse shaft
drilling, with diameters up to 2.4 meters and a monthly advance rate of 200–300
meters.
Ore Hoisting System: Uses wire rope hoisting systems to transport ore from
underground to the surface.
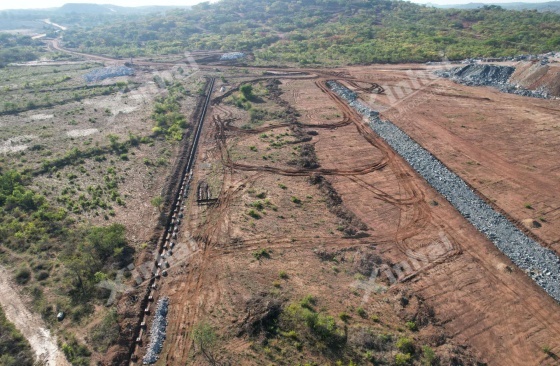
02Lithium Processing Equipment
1. Crushing and Grinding Equipment
Crushing Equipment: A jaw crusher is used for coarse crushing, while a cone
crusher is used for medium and fine crushing. Vibrating screens and auxiliary crushing equipment are used to classify and further crush lithium
ore. Ore with qualified particle size is sent to the grinding system.
Grinding Equipment: The crushed lithium ore is fed into a ball mill for
further grinding, typically to a particle size of -200 mesh. The spiral
classifier is used in combination to complete the grinding and
classification process.
2. Flotation Equipment
Agitation Tank (Slurry Agitator): After the initial ore
pretreatment, the ground slurry is mixed with water and flotation reagents in an
agitation tank to ensure thorough mixing before entering the flotation
machine.
Flotation Cell: Lithium-bearing minerals and gangue are
separated based on differences in floatability. During flotation, collectors are
adsorbed onto the surfaces of lithium minerals to make them hydrophobic and
float. Depressants (inhibitors), such as for quartz, feldspar, and mica, are
used to suppress gangue minerals, thus enabling effective separation.
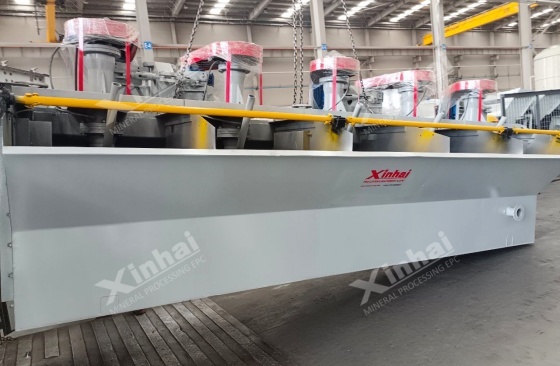
3. Dewatering Equipment
The lithium concentrate obtained from flotation is transferred to dewatering
equipment for moisture removal. Common equipment includes thickeners, vacuum
filters, and filter presses, which remove excess water from the concentrate
before the refining stage.
4. Tailings Dry Stacking Equipment
Different tailings dewatering solutions are applied based on the tailings'
particle size distribution:
Coarse-grained tailings settle quickly and are easier to dewater. A
combination of cyclone and high-frequency dewatering screen is typically used
for dry stacking.
Medium-grained tailings require enhanced solid-liquid separation and are
usually treated with a deep cone thickener followed by a plate and frame filter
press.
Fine-grained tailings, which are difficult to settle, require advanced
high-efficiency flocculation or high-pressure dewatering. A combination of a
high-efficiency thickener and ceramic filter is generally
employed.
03Lithium Equipment Model Selection Strategy
1. Processing Capacity
When selecting lithium mining equipment, it is essential to first determine
the required processing capacity and ensure it aligns with the mine's reserves.
If the capacity is too small, production targets cannot be met; if it is too
large, it will lead to unnecessary capital and operational costs.
2. Automated Control
Automated control systems not only reduce labor costs but also enhance
operational precision, minimizing the risk of resource waste due to human error.
Modern lithium processing plants are typically equipped with DCS (Distributed
Control System) and online monitoring systems to optimize flotation efficiency
and process stability.
3. Key Considerations for Selecting Flotation Equipment
As the core equipment in lithium ore beneficiation, choosing the appropriate
flotation machine is particularly critical. Important selection criteria include
air intake (aeration volume), agitation intensity, and corrosion resistance
(e.g., rubber lining or stainless steel construction).
4. Energy Consumption and Cost
Equipment with high energy consumption significantly increases operational
costs and reduces overall project profitability. Among all beneficiation
equipment, grinding mills typically consume the most energy. It is recommended
to select energy-saving ball mills, which can reduce power
consumption by up to 30% compared to conventional models, thereby lowering
electricity costs.
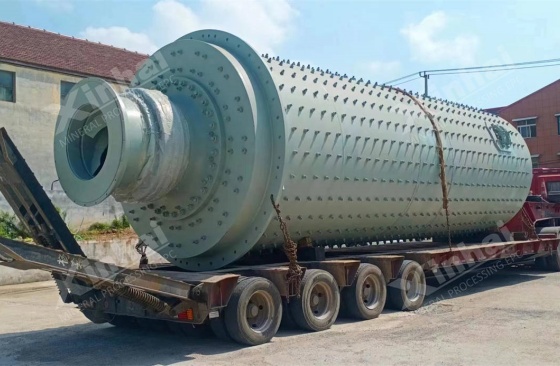
04Lithium Mining Equipment Manufacturer
Xinhai Mining is a professional provider of full-industry-chain lithium
mining and processing services, offering one-stop solutions covering lithium ore
exploration, design, equipment supply, construction management, and operations
(EPC+M+O).
Xinhai independently develops and manufactures lithium processing equipment,
including ball mills, flotation machines, thickeners, and more—suitable for hard
rock spodumene and lepidolite mines. These products are known for their high
efficiency, energy-saving performance, and intelligent design.
Xinhai’s EPC+M+O model integrates advanced mining and beneficiation
technologies, equipment manufacturing, and operation & maintenance
capabilities. It has been successfully applied in numerous lithium mining
projects worldwide, helping clients reduce investment risks while increasing
recovery rates and overall returns.
If you have any needs in lithium mining and processing, please feel free to
contact us.