The working efficiency of the ball mill equipment is related to many factors. The following mainly introduces you to several major influencing factors: ball mill structure, raw ore properties, rotation speed and filling rate, ball loading, ball mill cycle load, and grinding concentration.
Use the table of contents below to navigate through the guide:
01Influence of ball mill equipment structure
The diameter and length of the ball mill barrel have a great impact on its working efficiency. According to production practice, the productivity of a ball mill is directly proportional to its length and length. The larger the diameter and length of the cylinder, the higher its production efficiency. Therefore, large ball mills can be selected in large-scale mineral processing plants or when they need to improve the grinding efficiency of the mineral processing plant.
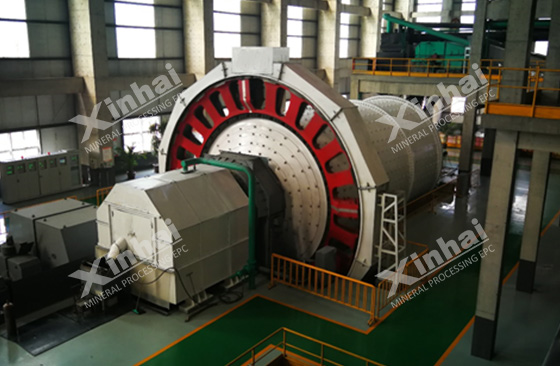
(ball mill)
02Influence of raw ore properties
The properties of raw ore mainly refer to the grindability of raw ore, the particle size of the raw ore and the mud content of the raw ore. If the same type of ore has different hardness and toughness, the production efficiency of the ball mill will also be different. The ore feeding particle size and grinding fineness also have a very important impact on work efficiency. When the required grinding fineness is the same, the feeding particle size decreases and the processing capacity of the ball mill increases. If the feed particle size is the same, the finer the grinding fineness, the lower the working capacity of the ball mill equipment. Therefore, reducing the feed particle size can be one of the measures to improve the working efficiency of the ball mill and reduce the grinding cost.
03Influence of ball mill equipment speed and steel ball filling rate
Filling rate and ball mill speed are two important factors that affect the working efficiency of the ball mill. Within a certain range, appropriately increasing the speed of the ball mill can improve the working efficiency of the ball mill. There is a certain relationship between the speed of the ball mill and the filling rate. As the filling rate increases, the rotational speed of the ball mill will decrease accordingly. At the same time, as the filling rate increases, the effective volume in the ball mill decreases, which in turn leads to a decrease in the working efficiency of the ball mill. Therefore, the appropriate filling rate should be selected according to the properties of the ore and the speed of the ball mill should be adjusted to improve the working efficiency of the ball mill.
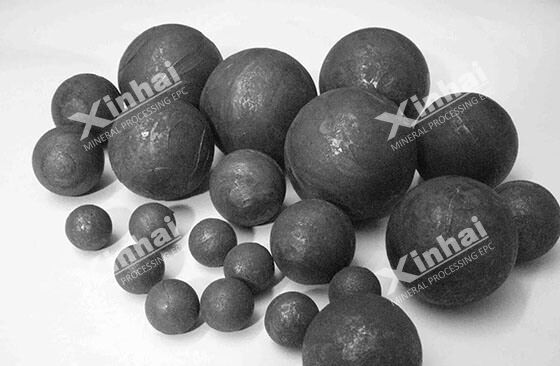
(Ball mill grinding media)
04Influence of ball mill equipment loading
The ball loading of the ball mill mainly refers to the ball quantity, billiard ball type and ball loading ratio. The type of ball loading mainly depends on the specific gravity of the balls, the particle size composition of the ore in the ball mill and the fineness of the product. Generally, as the ore becomes larger and harder, the ball diameter that needs to be filled should be larger. As the ball mill continues to operate, the balls in the mill continue to wear. In order to maintain the working efficiency of the ball mill when initially loading balls, it is necessary to keep the number, type and proportion of ball mills unchanged.
05Effect of cyclic load on ball mill
The ball mill generally forms a closed circuit with the classifier for grinding and classifying. The discharged ore from the ball mill is first sent to the classifier for processing. The qualified slurry overflows out, while the unqualified coarse particles are returned to the ball mill for re-grinding. This return sand is called circulating load. The percentage of these returned sand quantities to the original ore feed volume of the ball mill is the return sand ratio. Appropriately increasing the sand return ratio can shorten the time for the ore to pass through the ball mill, reduce the phenomenon of over-crushing and improve the production capacity of the ball mill. However, the total amount of mineral entering the ball mill should be strictly controlled, otherwise it will cause the ball mill to work out of order.
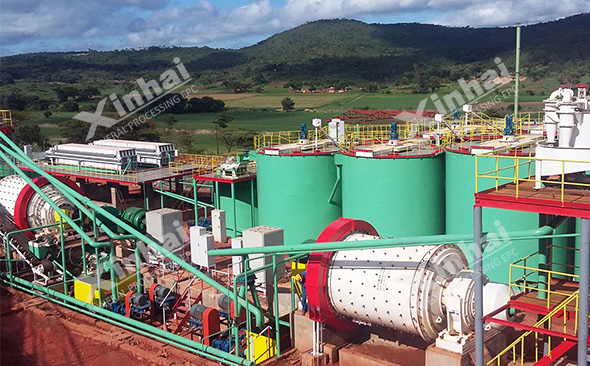
(Ball mill in mineral processing plant)
06Effect of grinding concentration
Grinding concentration is the ratio of water to ore in the ball mill. The grinding concentration mainly affects the friction between the ball and the ore, the fluidity of the slurry and the transportation capacity of the ball mill. When the grinding concentration is appropriately increased, the ore discharge volume will increase accordingly, so the working efficiency of the ball mill can be improved to a certain extent. However, when the grinding concentration is too high, the specific gravity of the slurry increases and the fluidity becomes poor, which reduces the grinding and peeling effect between the balls and the ore, thereby reducing the working efficiency of the ball mill. However, if the grinding concentration in the ball mill is too small, the effective ratio and mobility of the balls will increase, which will increase the grinding effect. However, if the concentration of the slurry is too thin and the slurry flows too fast in the ball mill, the coarse particles in the grinder will be brought out. At the same time, many mineral particles will be attached to the surface of the ball, thus affecting the grinding effect. Therefore, the appropriate grinding concentration should be selected based on the specific production requirements of the mineral processing plant.
The above are several factors that affect the working efficiency of the ball mill equipment. In actual production, the ball mill will be affected by both external and internal influences. The working parameters of the ball mill should be appropriately adjusted according to the specific production conditions to improve the working efficiency of the ball mill. At the same time, regular maintenance of the ball mill is also one of the measures to ensure and improve the ball mill.