A hydrocyclone is a device that utilizes centrifugal force for solid-liquid
separation, particle classification, or liquid-liquid separation. In iron ore
tailings processing, hydrocyclones play a significant role. They can not only
classify and concentrate tailings but also aid in the recovery of valuable
minerals. This article discusses the application of hydrocyclones in tailings
reprocessing, backfill preparation, and dry tailings stacking.
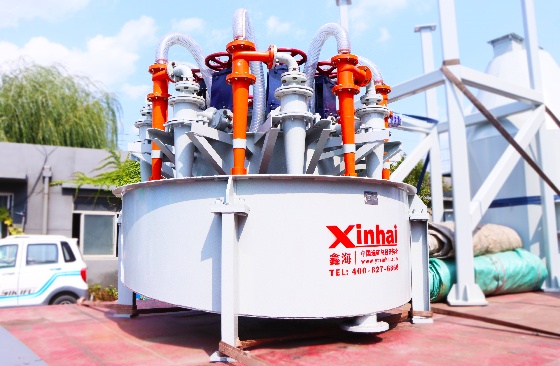
Use the table of contents below to navigate through the guide:
01Iron Tailings Reprocessing with Hydrocyclone Technology
1. Application Background of Hydrocyclones
The associated apatite (including P₂O₅) resources in certain iron ore
tailings can be recycled to generate economic benefits. However, traditional
methods such as magnetic separation and gravity separation are often ineffective
in recovering fine particles, leading to the loss of apatite in tailings
overflow and resulting in serious resource waste.
To enhance the recovery of apatite, a hydrocyclone was introduced into the
existing tailings treatment process to perform pre-classification on the
overflow. Fine apatite particles are concentrated into the cyclone underflow,
thereby reducing the interference of slimes during flotation and ultimately
achieving apatite enrichment and improved flotation efficiency.
2. Process Flow
Iron tailings → inclined plate thickener → overflow (containing fine apatite
slime) → hydrocyclone classification →
↓ (underflow, high-concentration apatite) → flotation →
phosphate concentrate
↓ (overflow, ultrafine slime) → tailings storage or further
reprocessing
3. Technical Advantages
Significantly improved classification efficiency reduces fine slime
entrainment in the underflow and minimizes reagent waste during flotation.
Cyclone-based pre-enrichment increases apatite grade by 10–15 times,
effectively lowering flotation costs.
Hydrocyclone models can be flexibly adjusted according to tailings particle
size, offering strong adaptability to different processing conditions.
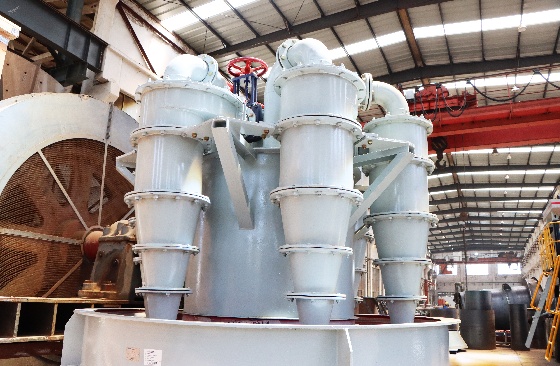
02Iron Tailings Backfill Process
1. Application Background of Hydrocyclones
Traditional full-tailings backfill technology faces two main challenges.
First, the backfill material often exhibits low strength due to a high content
of fine particles, which impairs cementation and results in insufficient
strength after curing. Second, the process incurs high costs, as a large amount
of cement is required to compensate for the poor strength, increasing material
expenses.
To address these issues, hydrocyclones are employed to classify and deslime
the tailings. This operation optimizes the particle size distribution and
concentration of the backfill slurry, thereby enhancing the strength of the
backfill material and reducing cement and other material costs.
2. Process Flow
Iron tailings → hydrocyclone classification →
↓ underflow (coarse particles, >20 μm) → backfill slurry
↓ overflow (fine particles,<20 μm) → tailings storage or reuse
3. Technical Advantages
Improved Backfill Strength:
By using hydrocyclones for classification, the backfill material consists
mainly of coarse particles, with a high proportion of >20 μm fractions. This
significantly enhances the strength of the backfill, fully meeting underground
support requirements.
Reduced Material Costs:
After removing fine particles with the cyclone, the tailings exhibit a more
favorable particle size distribution. This improves cement bonding efficiency,
reducing cement consumption by up to 30%, and directly lowering material
costs.
Simplified Process Flow:
The cyclone underflow can reach a concentration of 20%–25%, which is suitable
for direct use in backfill slurry preparation without the need for additional
thickening. This eliminates the thickening step of traditional processes,
reducing energy consumption and equipment investment.
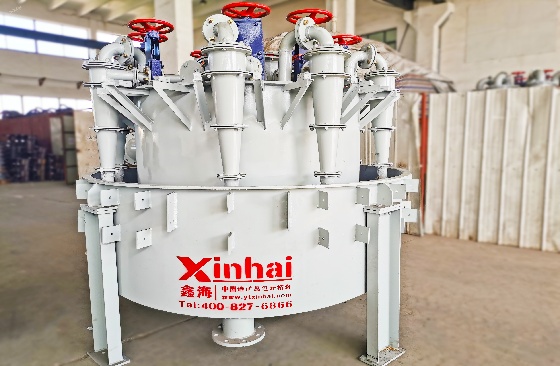
03Iron Tailings Dry Stacking Process
1. Application Background
The traditional method of tailings disposal involves discharging iron
tailings directly into tailings ponds for storage. This approach poses
significant safety risks and brings challenges such as limited storage capacity,
low return water utilization, and substantial water resource waste.
To address these issues, dry stacking of iron tailings is implemented. This
process utilizes hydrocyclones in combination with high-frequency dewatering
screens, deep cone thickeners, filter presses, and other equipment to achieve
efficient separation and solid-liquid management.
2. Process Flow
Iron tailings → hydrocyclone classification →
↓ coarse tailings → dewatering screens → dry stacking
↓ fine tailings → deep cone thickeners → plate and frame filter
presses → water recycling
3. Technical Advantages
Reduced Energy Consumption:
By pre-classifying tailings into coarse and fine fractions, the coarse
portion is directly dewatered and dry-stacked, while the fine portion undergoes
thickening and filtration. This separation reduces overall energy
consumption.
Water Conservation and Emission Reduction:
The water recycling rate exceeds 85%, with near-zero liquid discharge,
greatly conserving water and reducing environmental emissions.
Enhanced Safety:
The moisture content of tailings after dry stacking is less than 20%, meeting
the anti-liquefaction requirements for stacked tailings and improving tailings
storage safety.
Conclusion
This article has introduced the application of hydrocyclones in iron ore
tailings processing, particularly in three key areas: tailings reprocessing, dry
stacking, and backfill preparation. Hydrocyclones not only reduce environmental
risks and enhance flotation efficiency but also save water and lower operating
costs—making them an effective, dual-purpose solution.
Hydrocyclones produced by Xinhai Mining feature simple structure, high
processing capacity, and reliable performance. They are widely applied in iron
ore tailings treatment projects. If you are interested in purchasing, feel free
to contact us for more information.