Copper-cobalt ore serves as a primary raw material for extracting copper and
cobalt metals. In recent years, with the steadily increasing demand for these
two metals, copper-cobalt mining projects have drawn significant attention
worldwide. Flotation is the most commonly used method for the beneficiation of
copper-cobalt ores. This article outlines the flotation process for
copper-cobalt ore and presents a representative project case.
Use the table of contents below to navigate through the guide:
01Copper-Cobalt Ore Preferential Flotation Process
For copper-cobalt ores with significant differences in floatability and
minimal interference from gangue minerals such as pyrite, a preferential
flotation process is recommended. This method enables stepwise recovery of
copper and cobalt, resulting in a higher-grade concentrate. The flotation
process is as follows:
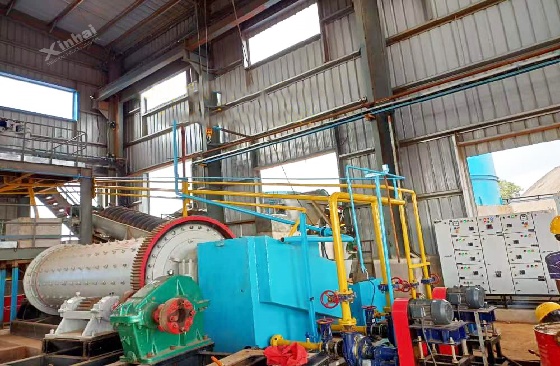
1. Ore Pretreatment
The copper-cobalt ore is first crushed and ground. Then, lime (CaO) is added
to the slurry to stabilize the pH in an alkaline range of 9–10. Lime serves to
inhibit the surface activity and floatability of gangue minerals such as
pyrite.
2. Copper Roughing
During the roughing stage, the collector YK1-11 is used. It is selectively
adsorbed on the surface of copper minerals to form a hydrophobic layer. MIBC is
used as the frother to regulate the stability of the froth layer. Bubbles
generated by aeration and agitation in the flotation cell carry the copper
minerals to the froth layer to obtain a copper rough concentrate.
3. Copper Cleaning (1–3 Stages)
The copper rough concentrate undergoes 1–3 cleaning stages to further improve
the concentrate grade by removing entrained gangue minerals and cobalt
minerals.
4. Cobalt Roughing and Cleaning
The tailings from copper flotation are used for cobalt recovery. Typically, a
multi-stage flotation process (roughing + scavenging + cleaning) is employed to
obtain a cobalt-sulfur concentrate. Butyl xanthate is added as the collector,
while MIBC or pine oil is used as the frother during cobalt flotation.
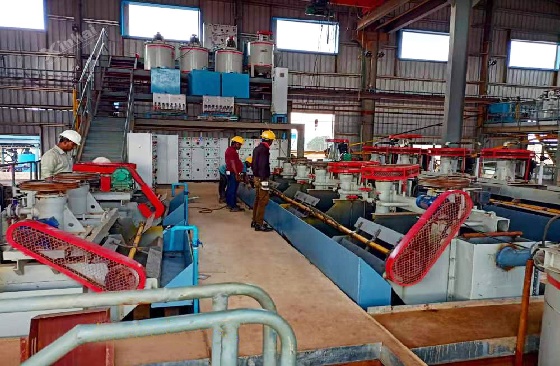
02Copper-Cobalt Ore Bulk Flotation Process
For copper-cobalt ores with complex mineral compositions, preferential
flotation cannot effectively separate copper and cobalt. In such cases, a mixed
flotation process combined with staged grinding is recommended. The specific
process is as follows:
1. Crushing and Primary Grinding
The run-of-mine ore is crushed to below 2 mm, and the grinding fineness is
controlled so that 60%–70% passes through 0.074 mm. At this stage, copper-cobalt
aggregates are partially liberated, though some intergrowths are still
allowed.
2. Rough Flotation
A reagent combination of butyl xanthate + BKNL + pine oil is used. The pulp
concentration is maintained at 25%–30%, and a copper-cobalt mixed rough
concentrate is floated.
3. Regrinding of Rough Concentrate
The mixed rough concentrate is further ground in a ball mill to break down
the intergrowth structures between copper and cobalt minerals, achieving a
monomer liberation rate of over 90%. A hydrocyclone closed-circuit system
ensures that coarse particles are returned for regrinding.
4. Multi-stage Cleaning
This stage aims to produce a high-quality copper-cobalt mixed concentrate.
Sodium silicate (Na₂SiO₃) is used to depress silicate gangue minerals, while
lime (CaO) maintains the desired pulp pH. After 3–4 cleaning stages, entrained
gangue is gradually removed, resulting in a purified copper-cobalt mixed
concentrate.
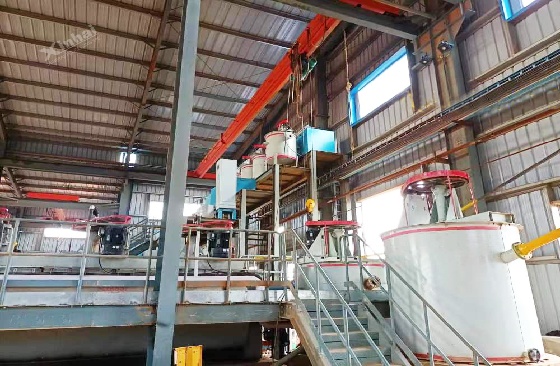
5. Copper-Cobalt Separation
A magnetic separation–flotation combined process is employed: iron is first
recovered from iron-bearing minerals via magnetic separation, followed by
flotation to separate copper and cobalt. For refractory ores with difficult
separation characteristics, hydrometallurgical methods may be adopted, with
copper and cobalt recovery rates exceeding 95%.
03Copper-Cobalt Ore Flotation Equipment
In the flotation process of copper-cobalt ore, the main operational stages
include crushing and grinding, flotation (roughing and cleaning), concentration,
and dewatering. The key equipment required for each stage includes
Crushing and Grinding: jaw crusher, cone crusher, ball
mill
Flotation (Sorting): slurry agitation tank,
mechanical agitation flotation cell/ flotation column, magnetic
separator
Concentration and Dewatering: flotation concentrate launder,
thickener, filter press / vacuum filter
In addition to this core equipment, various auxiliary equipment is also used,
such as vibrating screens, classifiers, hydrocyclones, slurry pumps, and belt
conveyors.
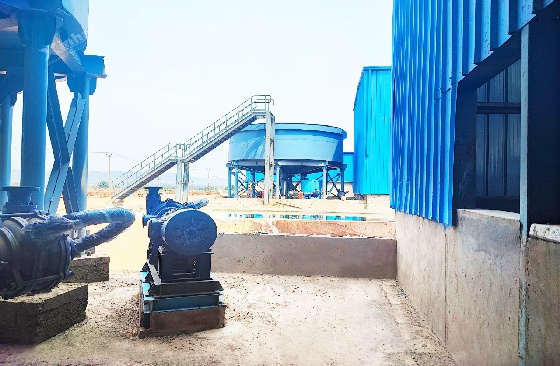
04Classic Case of Copper-Cobalt Ore Flotation
This project is located in the Democratic Republic of the Congo (DRC), and
the ore processed is highly oxidized copper-cobalt ore. Based on results from a
mineral processing test, a "cascading flotation + high-intensity magnetic
separation" process was selected. The flotation tailings were subjected to
magnetic separation for impurity removal.
Copper recovery rate reached 79.21%,Cobalt recovery rate was 33.33%.
After process optimization, the grade of copper concentrate increased by
1.09%, and cobalt concentrate by 0.03%.
This customized process—based on laboratory testing and combining flotation
with magnetic separation or hydrometallurgy—enabled the efficient recovery of
copper and cobalt resources, while also reducing mineral processing costs.
Conclusion
With the continued exploitation of copper-cobalt resources, low-grade
copper-cobalt ores will become a key focus of future beneficiation efforts. The
formulation of scientific, cost-effective beneficiation flowsheets and the use
of high-performance, intelligent mineral processing equipment will be critical
to ensure project feasibility and profitability.
Xinhai Mining provides EPC+M+O services—a closed-loop solution covering
mineral processing test, process design, equipment supply, installation &
commissioning, and plant operation—ensuring target production is achieved within
a fixed cost and schedule.
If you are interested in this solution, feel free to contact us!