Kaolin is widely used in ceramics, papermaking, coatings, rubber, and other
industries. In recent years, with the rapid development of emerging sectors, the
demand for kaolin in electronic ceramics, specialty coatings, and high-grade
papermaking has grown significantly. Ensuring high purity and stable quality of
kaolin has become a key challenge for suppliers. Xinhai Mining provides
comprehensive solutions covering the entire process—from mining to
beneficiation—ensuring the quality of kaolin products from the source. This
article presents a complete guide to the kaolin mining and beneficiation
process.
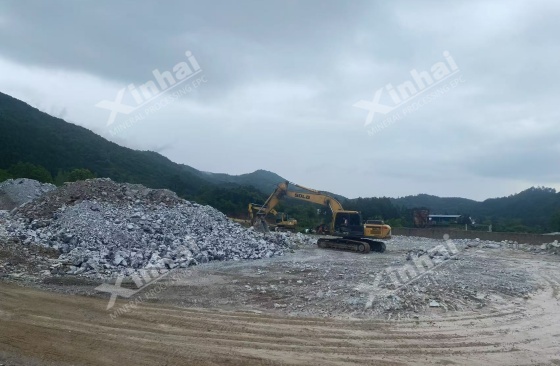
Use the table of contents below to navigate through the guide:
01Kaolin Mining Process
1. Exploration and Planning
Geological Exploration: Identify the location, scale, grade,
and occurrence conditions of the kaolin ore body. Utilize hyperspectral remote
sensing technology to shorten the exploration cycle and increase proven
reserves.
Design and Planning: Based on exploration results, conduct a
feasibility study and develop a mining plan for kaolin. The plan typically
includes mining boundaries, mining sequence, transportation routes, and other
key parameters.
2. Pre-Mining Preparation
Site Leveling: Involves vegetation removal, topsoil
stripping, obstacle clearing, and other operations to form a stable working
platform capable of supporting heavy equipment.
Infrastructure Construction: Construct main and temporary
access roads in the mining area, establish the primary power supply network,
configure backup power systems, and plan water supply and drainage systems.
3. Mining
Select open-pit or underground mining methods based on the ore body’s
occurrence conditions and the mine’s production scale.
(1) Open-Pit Mining:
Suitable for kaolin deposits with shallow ore bodies, large scale, and stable
rock conditions. The process includes:
Removing topsoil and overburden using excavators, loaders, and other
equipment to expose the ore body
Drilling blast holes and using explosives to fragment the ore
Loading and hauling the broken kaolin ore to the processing plant or ore
stockyard using dump trucks
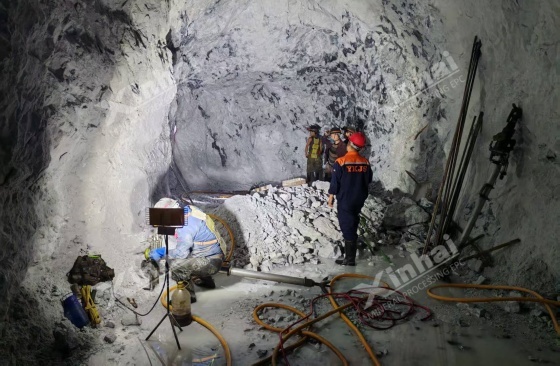
(2) Underground Mining:
Applicable to deep-seated kaolin deposits with smaller scale and less stable
rock conditions. The process includes:
Driving tunnels around the ore body; tunnel types may include adits, inclined
shafts, or vertical shafts depending on the ore body orientation
Developing production tunnels within the ore body
Conducting drilling and blasting using rock drills
Transporting broken ore to the surface via loaders or mine carts
Ventilation and drainage systems must be in place to ensure operational
safety underground.
4. Environmental Protection
Implement slope stabilization measures to prevent landslides and collapses.
After mining operations conclude, conduct land reclamation and restore
vegetation to minimize environmental impact.
02Kaolin Processing Flow
The mined kaolin ore must undergo further processing to improve its purity
before it can be applied in downstream industries. The kaolin processing flow
includes the following steps:
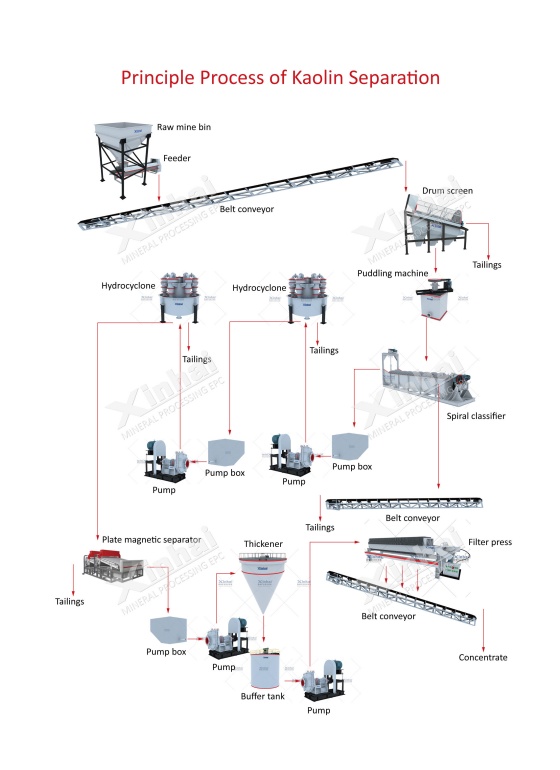
1. Crushing and Grinding
The kaolin ore is first sent to a jaw crusher for primary crushing, reducing
the particle size to ≤100 mm. Next, a cone crusher performs secondary and fine
crushing, reducing the size to ≤30 mm. Throughout the crushing stage, vibrating
screens are used for particle size classification. Qualified materials proceed
to the grinding stage, while oversized particles are returned for further
crushing.
The crushed ore then enters the grinding process, which is typically
integrated with hydrocyclones or spiral classifiers for classification.
Oversized particles are returned for regrinding. The choice of grinding
equipment depends on the intended application of the final product:
Ball mills are used for ordinary filler-grade kaolin,
Stirred mills are used for coating and papermaking-grade,
Jet mills (airflow mills) are used for high-purity electronic ceramic-grade
kaolin.
2. Purification and Impurity Removal
Flotation: Dodecylamine is added as a collector, and sodium
hexametaphosphate as a dispersant and quartz depressant. Mechanical agitation
flotation is used to remove TiO₂.
Magnetic Separation: A high-gradient magnetic separator is
employed to reduce Fe₂O₃ content from 1.8% to 0.35%.
Gravity Separation and Classification: The slurry is
classified using a hydrocyclone. The first stage removes coarse particles (+325
mesh), and the second stage classifies ultrafine particles (−2 μm). A spiral
chute is used to enhance kaolin purity.
3. Chemical Bleaching
In the first method, sodium dithionite is added, with pH controlled at 3–4
and temperature maintained at 60 °C. This process can increase the whiteness of
kaolin to 92%, but it generates wastewater requiring treatment.
In the second method, ozone oxidation is applied to the concentrate slurry,
with an ozone concentration of 50 ppm at room temperature. This method can
increase whiteness to 90%, and it is environmentally friendly with no harmful
residues.
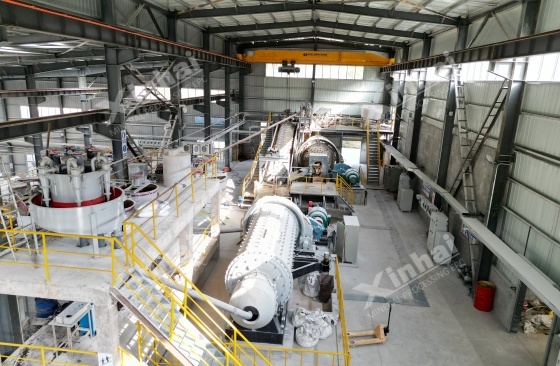
4. Drying and Packaging
After beneficiation and bleaching, the kaolin is dried and packaged for sale.
The drying method is selected based on the end use:
For coating and ceramic-grade kaolin, spray drying is used (moisture
≤1%).
For rubber and plastic-grade, flash drying is preferred (moisture ≤0.5%).
For pharmaceutical and food-grade, belt drying is employed (moisture
≤0.3%).
03Kaolin Product Quality Control
Kaolin processing involves a complex flow with more than 20 procedures. Due
to factors such as ore composition fluctuations, process parameter drift, and
equipment wear, the whiteness, viscosity, and particle size of the final product
can vary from batch to batch. Therefore, stabilizing product quality is of
critical importance.
Xinhai Mining has achieved a breakthrough in product stability through a
"three-in-one" quality control system:
Source Control:
The raw ore composition fundamentally determines product quality. During
beneficiation testing, an X-ray fluorescence (XRF) online analyzer is used to
monitor the ore composition in real time. The processing parameters are then
adjusted based on the specific mineral composition to ensure consistency.
Process Control:
PLC (Programmable Logic Controller) automatic control systems are deployed at
critical stages such as grinding and flotation to maintain particle size
deviation within ±0.3 μm.
Final Quality Assurance:
Each batch of products undergoes six comprehensive inspections, enabling
precise tracking and monitoring of product quality.
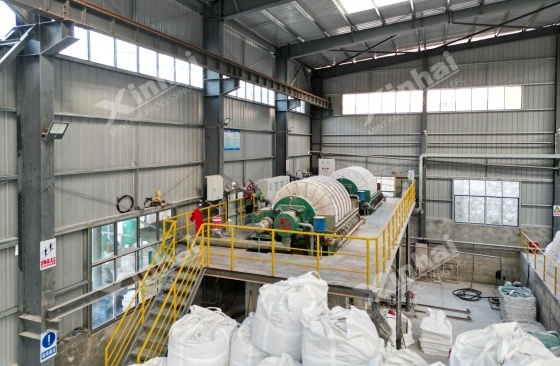
Conclusion
This article has introduced the kaolin mining process, beneficiation
techniques, and quality control strategies. Xinhai Mining offers complete EPC+M+O
services for kaolin-related mining and mineral processing projects. For further
inquiries or cooperation, please feel free to contact us.