As medium- and high-grade copper-molybdenum deposits become increasingly
scarce, low-grade resources have become the primary targets for extraction. As a
professional mining service provider, Xinhai delivers comprehensive
open-pit mining solutions by integrating core technologies such
as geological modeling, mine planning optimization, and intelligent mining
equipment. This article outlines the methodologies used in open-pit mining of
low-grade copper-molybdenum ore.
Use the table of contents below to navigate through the guide:
01Geological Modeling and Resource Assessment
Xinhai utilizes 3D geological modeling software to construct detailed
geological and economic models. On platforms such as Datamine, the
Lerchs–Grossmann (L-G) algorithm is employed to convert parameters—such as the
spatial distribution of ore bodies and ore selectivity—into economic indicators,
enabling dynamic optimization of the mine plan.
The equivalent grade method is applied to assess the value of
copper-molybdenum co-occurring ores. The economically minable resource
boundaries are defined using parameters such as metal prices and ore recovery
rates (copper ≥ 85%, molybdenum ≥ 75%). For instance, at a copper-molybdenum
project in Tibet, the cut-off grade was lowered by 0.015%, resulting in 23
million additional tons of economically recoverable ore.

02Pit Limit and Mining Boundary Optimization
The product cost comparison method, combined with a dual-index verification
system based on strip ratio analysis, ensures that stripping costs remain below
the economic threshold of ore value. Using the Whittle four-dimensional
optimization algorithm, the economic viability of different slope angles
(45°–55°) and bench heights (12–15 m) is simulated within the geological model
to identify the optimal mine design.
03Semi-Continuous Mining Process for Low-Grade Copper-Molybdenum Ore
A mobile in-pit crushing station is deployed within the mining area. By
monitoring the advance rate of the working face in real time, the station’s
layout spacing is dynamically adjusted.
At one copper-molybdenum project, the average truck haulage distance was
reduced to 1.2 km by optimizing the relocation schedule, resulting in a 28%
decrease in transportation energy consumption compared to a conventional fixed
crushing system.
To tackle challenges in the ore–waste contact zones, a selective mining and
separate haulage strategy is adopted. A trench is first developed along the ore
body, and two sets of mining equipment are assigned separately for ore and waste
handling. This strategy maintains the ore loss and dilution rates within 3%.
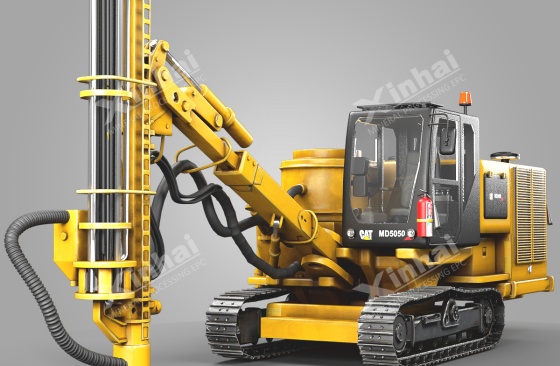
04Construction of a Dynamic Grade Management System
We have developed an intelligent boundary grade control system and
established a dynamic economic model based on parameters such as metal prices
and production costs.
In one molybdenum mine project, the maximum profit per ton method was
applied. When the molybdenum price reached 170,000 yuan/ton, the cut-off grade
was raised from 0.05% to 0.078%, increasing the concentrate profit margin by 14
percentage points.
For debt-free mines with sufficient capital, the maximum total profit method
is adopted. By lowering the cut-off grade by 0.004 percentage points, the
economically recoverable ore increased by 12.05 million tons, and the mine’s
service life was extended by 3.6 years.
05Copper-Molybdenum Mining Equipment and Mining Strategy
In terms of equipment selection, we recommend using a 12 m³ electric shovel
paired with a 90-ton dump truck to form a standard mining and hauling unit, with
each unit capable of processing 8 million tons of ore annually.
A zoning and phased mining strategy is applied to complex ore bodies.
High-grade ore near the surface is mined first, while a progressive stripping
scheme is adopted for low-grade mixed zones. By implementing this strategy, a
mine in Central Asia successfully delayed the stripping peak during the first
three years, saving 230 million yuan in upfront investment.
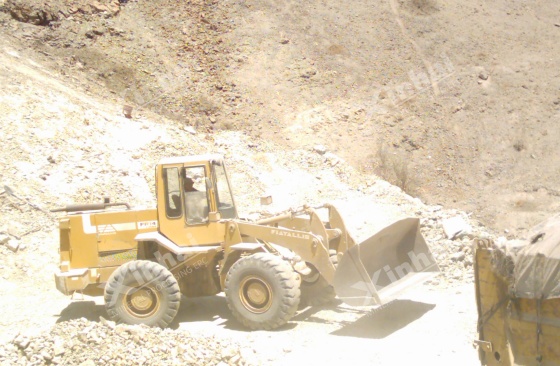
06Mineral Processing Technology for Low-Grade Copper-Molybdenum Ore
For copper-molybdenum ore beneficiation processing, we have
developed a “bulk flotation followed by copper-molybdenum separation” process.
After the copper-molybdenum bulk concentrate undergoes thickening and impurity
removal, nitrogen inflation flotation is employed to selectively depress copper
sulfide minerals, stabilizing the molybdenum concentrate grade above 52%.
When this method was applied to a low-grade copper-molybdenum deposit,
recoverable resources increased by 23%, and the cut-off grade was lowered by
0.012 percentage points. In addition, the introduction of microwave-assisted
heating in the pretreatment stage improved the collector’s decomposition
efficiency by 40% and reduced reagent costs by 18%.
Conclusion
As a professional mining service provider, Xinhai Mining offers full-process
EPC+M+O services in mining and mineral processing. Our projects have been
implemented in over 100 countries and regions worldwide, delivering tangible
economic benefits to many low-grade copper-molybdenum operations. With the
continued advancement of automation and intelligent technologies, Xinhai is
committed to providing even more efficient and intelligent mining solutions.